Ultrasonic Cleaner Learning Center
From the right tank size to degassing the cleaning solution for maximum efficiency, these short crisp videos will teach you everything you need to know to get the most out of your ultrasonic cleaners.

Introduction to Ultrasonic Cleaners
Ultrasonic cleaners produce cavitation action in predominantly water-based biodegradable cleaning solution chemistries. The process is widely used to remove contaminants from virtually any product that can be safely immersed. Ultrasonic cleaning is faster, safer and more effective than manual cleaning using brushes with potentially harmful solvents in wash tanks or using aerosol sprays.

Ultrasonic Tank Size
An ultrasonic cleaner must be large enough to handle what is being cleaned. But the critical measurement is the size of the ultrasonic cleaning basket that holds the part(s). This is because basket dimensions are slightly less than the inside dimension of the ultrasonic cleaning tank. Working depth is important because parts being cleaned must be fully immersed in the cleaning solution.

Why Use Parts Baskets
Ultrasonic cleaner baskets serve many functions. One of the most important is to protect the tank from damage due to parts vibrating against the bottom. This also dampens the ultrasonic frequencies. Cleaning baskets facilitate placing and removing parts in the cleaning solution, especially when multiple parts are cleaned in one cycle.
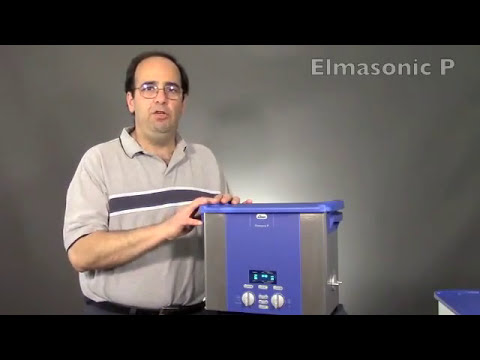
Elmasonic Benchtop Models
Three Elma benchtop ultrasonic cleaner models are available in several sizes and are differentiated by features, not by quality or warranty. Elmasonic E is the basic line delivering effective ultrasonic cleaning for a wide range of parts. Higher power and faster cleaning, along with additional flexibility in terms of three operating modes for cleaning, degassing, and mixing, are packaged with the Elmasonic S series. The advanced benchtop P line delivers additional flexibility in terms of adjustable ultrasonic power and dual-frequency 37 or 80 kHz sonication.

Ultrasonic Sweep Mode
The sweep mode in an ultrasonic cleaner provides a slight shift in frequency such as ± 3 kHz over the unit’s operating frequency. This promotes more uniform and more thorough cleaning especially for delicate parts and parts with complex shapes. The Sweep mode also avoids what are called hot spots or standing waves of intense ultrasonic energy, and dead zones where there is no cavitation action. Without Sweep the cleaning process can result in streaking or otherwise damaging highly finished surfaces.

Cleaning Solutions
Cleaning solution chemistry is specified based on what is being cleaned and contamination being removed. Most solutions today are biodegradable, non-toxic, and highly concentrated so a little goes a long way. Three common water-based families are alkaline, acidic, and neutral with different formulations to suit specific requirements. Solutions formulations are also available for specialized cleaning requirements such as optics, weapons and medical instruments. Flammable solvents require an explosion-proof cleaner.

Heated Ultrasonic Cleaners
Heated ultrasonic cleaning solutions are recommended for removing oil, grease, machining coolants and similar contaminants. Heater-equipped ultrasonic cleaners provide temperature control to 80⁰C or about 180⁰F. Higher temperatures usually stop cavitation action. Heating is not recommended when cleaning medical instruments contaminated with blood or biological tissue. Cleaning solution instructions provide temperature recommendations.

Ultrasonic Cleaner Accessories
Accessories add to the utility of your ultrasonic cleaners, starting with the cleaning basket to hold the products and the lid to slow solution evaporation, dampen sound and serve as a drip tray. Fine mesh baskets are available when cleaning small parts. Blending, dissolving and dispersing are facilitated when suspending samples in the bath using Erlenmeyer flask holders, test tube holders or specially designed lids to hold beakers. If high bath temperatures are a concern a cooling coil attached to a cold water line serves as a heat exchanger.

Ultrasonic Frequency
Ultrasonic frequency determines the size of the cavitation bubbles, with higher frequencies equating to smaller bubbles. Bubble size determines cleaning capability. Larger bubbles created by lower frequencies such as 25 kHz are best for coarse cleaning whereas higher frequencies such as 37 kHz and above are better for fine cleaning. Dual frequency ultrasonic cleaners are available for a broad spectrum of cleaning requirements.
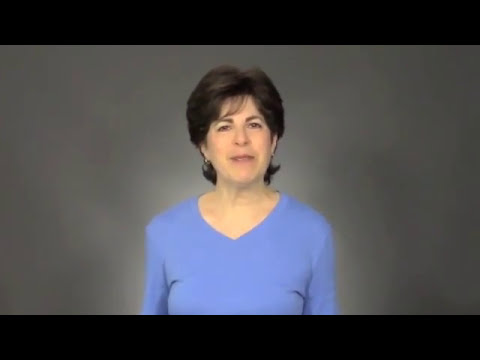
Ultrasonic Degassing
Removing entrapped air or dissolved gases from fresh ultrasonic cleaning solutions makes ultrasonic cavitation more efficient. An ultrasonic cleaner equipped with a degas mode accomplishes this faster than operating a non-equipped cleaner without a load. Degassing is accomplished when the ultrasonic cleaner cycles on and off. Air bubbles form in the “on” cycle. During the “off” cycle they rise to the surface and burst.
Your Time Is Important |
Our PhD support staff are experts at finding the perfect cleaner for your needs and budget Calls normally last less than 5 min! (973) 913-9734or |