How Do Ultrasonic Cleaners Work?
A simple way to illustrate how an ultrasonic cleaner works is likening them to an automatic dishwasher, but with some added refinements. An automatic dishwasher, much the same as an ultrasonic cleaner, combines water and a detergent to remove grease, grime and other contaminants from objects being cleaned.
Applications for ultrasonic cleaners include cleaning precision optics and laboratory glassware. Instead of cleaning pots and pans and bowls, ultrasonic cleaners most often are used to clean various other metal and plastic products difficult or impossible to clean by other methods.
How an Ultrasonic Cleaner Works
Unlike high-pressure water sprays used in automatic dishwashers, ultrasonic cleaners work by using the power of imploding (not exploding) minuscule bubbles in a process called cavitation. This process is explained below. Also different is the use of biodegradable cleaning solution concentrates specially formulated for the cleaning tasks at hand. You can learn more about how these work in our post on how to select a cleaning solution formula. Use instructions for these solutions are provided by the manufacturers.
Components of an Ultrasonic Cleaner
Understanding how an ultrasonic cleaner works calls for an understanding of their components. A Google search for these cleaners will reveal that models and pricing range all over the map. At the basic, however, these units consist of:
- Tanks to hold the cleaning solution. Tanks should be of stainless steel; their volume depends on the size of objects being cleaned
- Ultrasonic transducers that create the cavitation and that are bonded to the bottom of the tank
- A generator to power the transducers
- Controls that range from a simple on-off switch to sophisticated microprocessors that govern cleaning time, sweep, pulse, degassing, temperature, ultrasonic frequency , ultrasonic power, auto safety shutoffs and other refinements. More on these below.
These cleaners range from small tabletop units to huge, multi-gallon industrial cleaners. The capacity of the cleaners has little or no bearing on the features they can offer - desired feature decisions are up to the purchaser.
What Do Ultrasonic Transducers Do?
There are two basic types of transducers; piezoelectric (a.k.a. electrostrictive) or magnetostrictive, but their function is the same. They are excited by electric current provided by the ultrasonic cleaner's generator to vibrate at ultrasonic frequencies that cause the bottom (and sides as the case can also be) of the tank to vibrate and thus serve as a membrane. This vibration forms the vacuum bubbles that implode, (not explode) on contact with items in the ultrasonic cleaner tank thereby blasting loose and carrying away contaminants. There are also immersible transducers. Ultrasonic frequency is an important part of how an ultrasonic cleaner works and is discussed next.
How to Choose an Ultrasonic Cleaner Frequency
Ultrasonic is typically defined as sound above the human range of hearing. Low frequencies such as 25,000 cycles per second or 25 kHz produce relatively large bubbles that implode more violently than those created at higher frequencies such as 37, 80 or 130 kHz that produce progressively gentle cleaning action. As an example, the radius of a cavitation bubble produced at 37 kHz is approximately 88 microns. At 80 kHz it is 41 microns.
As a bit of digression, the implosion of cavitation bubbles produce shock waves radiating from the site of the collapse and create temperatures in excess of 10,000°F and pressures in excess of 10,000 psi at the implosion site. Yet the process is so fast that there is little heat buildup and no damage to parts being cleaned. That said, one should never reach into an operating ultrasonic cleaner to check, reposition or remove parts for examination.
Removing gross contaminants from robust parts such as fabricated or cast metals requires lower frequency cleaners. Softer metals, plastics, and products with polished surfaces should be cleaned at higher frequencies. In addition to protecting polished surfaces smaller bubbles are better able to penetrate tight areas such as seams, crevices and blind holes. If you'd like more information on this particular topic check this article on selecting ultrasonic cleaner frequencies.
Our point is that purchasing decisions for an ultrasonic cleaner should be made on more than price.
Why You Need an Ultrasonic Cleaner Basket
Ultrasonic cleaners work best when cavitation bubbles access all surfaces immersed in the cleaning solution. This is best accomplished when parts are suspended in the solution, not reposing on the cleaning tank floor. In the majority of instances, baskets are used to hold the parts at the proper distance from the tank bottom. Baskets typically are of stainless steel mesh with mesh or solid stainless-steel walls. Small parts such as screws can be placed in fine mesh baskets that either rest in the tank basket or are suspended in the solution. Very large parts can be suspended from overhead supports to the correct depth for cleaning.
Why is this? In addition to promoting more efficient cleaning baskets keep parts from contact with the tank bottom where ultrasonic frequency vibrations cause wear to the tank. Eventually this may lead to holes being developed in the tank and vibration damage to the parts being cleaned.
This brings up a point when considering the size (tank dimensions) of your ultrasonic cleaner. Ultrasonic cleaners work best when parts are totally immersed in the solution. Other than obvious width and length of the tank (more specifically the basket) is what is called the working depth of the unit, or the distance between the bottom of the basket and the surface of the cleaning solution. Keep that in mind when selecting your unit.
An Explanation of Ultrasonic Cleaner Bells and Whistles
Ultrasonic cleaners work best when they provide features that make the cleaning faster, more thorough and hence more efficient. Earlier we mentioned that basic units may be equipped only with a simple on-off switch, but indicated other features that can lead to the desired results. Here is a brief rundown of those:
- Timers let you program the length of the cleaning cycle (often gained through experience) so you can set the time and do other tasks while cleaning takes place.
- Temperature controls let you set the recommended cleaning temperature as recommended by the cleaning solution provider. Some units are equipped to provide auto-start when the set temperature is reached.
- Sweep Mode provides a slight ± variation in ultrasonic frequency that avoids what are called hot spots (potentially damaging high cavitation), dead zones (low or no cleaning action) and harmonic vibration that can damage delicate parts such as printed circuit boards. The opposite of Sweep is Normal, or fixed frequency, which has use in labs for sample preparation. Some units offer a choice of Sweep and Normal.
- Degas Mode drives off trapped air in fresh cleaning solutions. Trapped gas interferes with cleaning action. Running the unit without a load will eventually degas the solution but takes longer.
- Pulse Mode delivers pulses of increased ultrasonic power to blast away tenacious contaminants. Pulse can also be used to degas solutions.
- Ultrasonic frequency can be varied on certain units, letting users set the frequency best-suited for the job and thereby broadening the use of their ultrasonic cleaner. Examples are 25/45 kHz, 35/130 kHz and 37/80 kHz
- Ultrasonic power is controllable on certain models, also letting users set the best cleaning parameters for the jobs at hand. These usually allow increments from 10 to 100%.
- Safety shutoffs help protect the unit and contents against excess temperatures and overlong cleaning cycles that may cause cleaning solution evaporation below recommended levels.
There are many accessories offered by manufacturers that help ultrasonic cleaners work better and more efficiently. Examples include soundproof covers, cooling coils, flask holders and for larger units, cleaning solution filters, covered in part next.
Where do Ultrasonic Cleaning Contaminants Go?
For the automatic dishwasher, the answer is down the drain. For your ultrasonic cleaner, they remain in the solution. Contaminants removed during the cleaning process either float to the surface or sink to the bottom or remain in suspension. Our earlier reference on cleaning solution selection goes into this in some detail.
Contaminants that float to the top should be skimmed off and set aside for later disposal. Some tanks are equipped with skimmers and weirs to direct floating contaminants to a collector. Large units can be equipped with filters to extend solution life.
The point is, eventually efficiency will fall and the solution must be drained and disposed of along with skimmed off contaminants, according to local regulations.
When that time comes take the time to clean your ultrasonic cleaner tank following the manufacturer's instructions. Prepare and degas fresh solution and you're ready to resume cleaning.
Contact the ultrasonic cleaning professionals at Tovatech for help in selecting the ultrasonic cleaner and cleaning solution combinations that work best for your operations.
Useful Resources on How an Ultrasonic Cleaner Works
View our ultrasonic cleaning learning center videos to learn everything you need to know to get the most out of your ultrasonic cleaners.
Check out our blogs for more examples of how folks use ultrasonic cleaners.
Get Expert Advice on Ultrasonic Cleaners |
Our PhD support staff are experts at finding the perfect cleaner for your needs and budget. It takes less than 5 min! (973) 913-9734or |
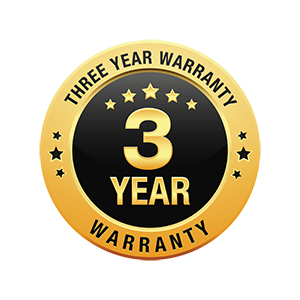
Elma 3 Year Warranty
Elma stands behind their products. All Elma ultrasonic cleaners come with an industry-best 3 year warranty. If the unit malfunctions because of a manufacturing defect, simply call us and we’ll repair or replace the unit.
Looking for Pricing? |
![]()
Download our |