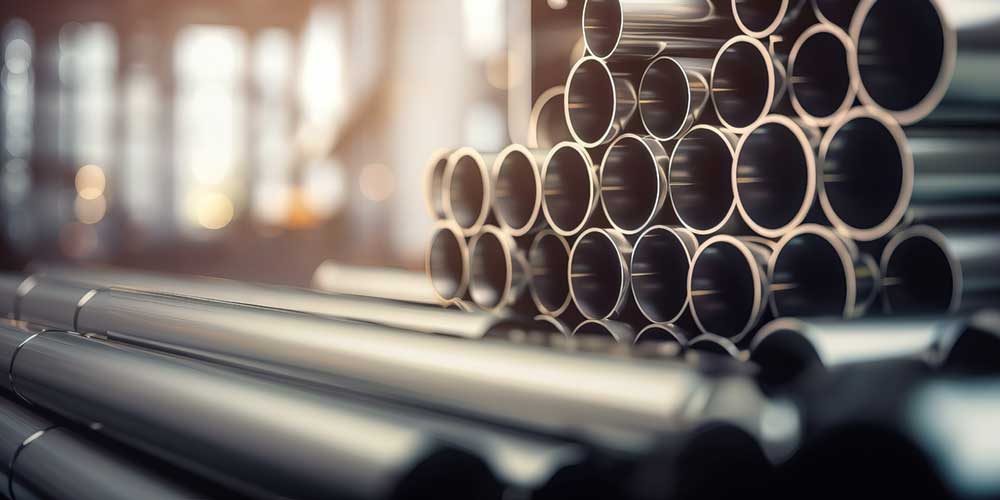
Ultrasonic Passivation for Stainless Steel
Stainless steels such as AISI* Types 304, 310 and 316, are favored for strength and corrosion resistance. Applications include food, chemical and pharmaceutical processing, surgical implants, architecture and transportation. Over time starting from initial fabrication, free iron and other contaminants adhere to surfaces and must be removed. Ultrasonic passivation for stainless steel accomplishes this to meet ASTM** A967 standards.
What is Stainless Steel “Passivation?”
Machining and otherwise fabricating and handling stainless steel components may deposit iron particles and other contaminants (such as from machining or grinding tools) on the stainless steel. These contaminants must be removed to forestall corrosion between the different metals once the stainless steel components are put into use.
Passivation removes these contaminants, forming a “passive” oxide film that becomes a chemically inactive or inert surface that enhances corrosion resistance.
Passivation vs. Electropolishing
There is some confusion between passivation and electropolishing as both relate to treating stainless steel components. Electropolishing, as the name suggests, is an electrochemical process used to remove roughness or unevenness to achieve an ultra-smooth surface – hence “polishing.” Passivation, when required, usually is employed after electropolishing or in instances where electropolishing is not performed.
Benefits of Ultrasonic Passivation
The very benefits that make ultrasonic cleaners so widely accepted across such a wide range of applications apply as well to ultrasonic passivation.
In fact, ultrasonic cleaning finely machined and fabricated stainless steel components may – or perhaps should – precede ultrasonic passivation.
Pre-cleaning before passivation helps assure you that metal fines, machining oils and other contaminants are not introduced into the stainless steel passivation bath. A good cleaning solution formulation for this procedure is elma tec clean A4 diluted to 2 to 5% with water.
Following this process the next step is passivation. Here we offer two options.
Two Ultrasonic Passivation Options
Ultrasonic passivation can be accomplished using either a nitric acid or citric acid bath.
Stainless Steel Passivation with Nitric Acid
Nitric acid is the “traditional” process but – and an important “but” – it is a highly dangerous acid. Its use requires special procedures to deal with toxic gases, elevated temperatures and serious environmental concerns both in use and eventual disposal.
These concerns have increased significance because the ultrasonic passivation process by its nature heats the cleaning solution – further increasing evaporation emissions. These must be dealt with by providing ventilation systems in close proximity to the ultrasonic passivation tank.
Personnel using nitric acid must comply with OSHA-related safety procedures as well.
In addition to these precautions, nitric acid passivation baths can damage then destroy ultrasonic passivation tanks unless an acid resistant tank liner is employed. These are available in several sizes to fit within the tanks of benchtop ultrasonic cleaners. Ultrasonic energy passes through the liner to act on its contents.
Citric Acid Stainless Steel Passivation
Many of the drawbacks of nitric acid passivation are eliminated when using a citric acid bath for the process.
While a little more costly than nitric acid, using citric acid for stainless steel passivation (even by the inference of its name) is far less hazardous. On the plus side, in addition to being usable at room temperature it is faster, requires lower concentrations, and is environmentally friendly.
There is no need to select and purchase an acid-resistant tank liner.
Moreover, selecting citric acid passivation does not mean squeezing oranges, grapefruits, lemons and limes into your ultrasonic passivation tank for stainless steel.
Instead we recommend mildly acidic elma tec clean S1 diluted to 10 to 20% with water to do the job. Follow directions on the accompanying product information sheet.
Selecting Ultrasonic Stainless Steel Passivation Equipment
Your company, the products you provide and the standards with which you must comply will guide your decision on using a nitric or citric passivation solution for stainless steel. Another decision is how to select the equipment you need to perform the ultrasonic passivation process.
The important consideration is part size and dimensions. Next is throughput – that being how many parts must be handled over a period of time.
Keep in mind that stacking parts into an ultrasonic passivation tank is NOT recommended. Select a unit that will handle part size, quantity and throughput you need to assure maximum productivity without damaging your company’s reputation.
For companies dealing with relatively small parts, Tovatech offers a broad range of benchtop ultrasonic cleaners, some of which will accommodate liners that accept nitric acid passivation.
Our industrial ultrasonic cleaners, both benchtop and floor mounted mobile units, are best-suited for a citric acid cleaning solution such as the recommended elma tec clean S1.
Need More Info on Stainless Steel Passivation?
There are several considerations to ponder when you are looking for a unit to accomplish ultrasonic passivation for stainless steel. Or for that matter any other product requiring cleaning or passivation. For this we direct your attention to our post 5 points for selecting correct ultrasonic cleaner size.
Chat or call the Tovatech scientist for unbiased advice on equipment, options and cleaning solution formations that match your requirements to meet local and industry standards.
—————————–
*American Iron and Steel Institute
** American Society for Testing and Materials