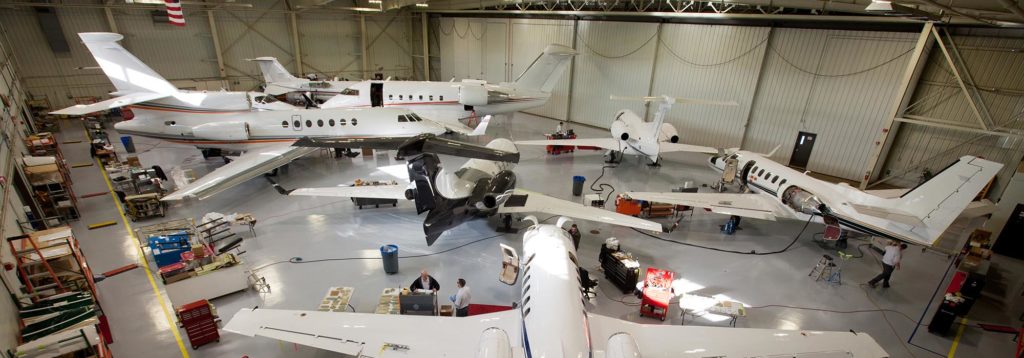
Ultrasonic Cleaners for Jet Engine Maintenance
Regular maintenance procedures are strictly prescribed for aircraft jet engines and include thorough cleaning and inspection of fuel nozzle assemblies. “An example is the highly popular Pratt & Whitney PT6A engine which requires cleaning engine fuel nozzle manifold adapter assemblies every 400 hours of operation,” says Scott Pottebaum, Director of Technical Services, Elliott Aviation in Des Moines, IA. “Overhaul and maintenance procedures are clearly spelled out in the P&W Maintenance Manual; service organizations such as Elliott Aviation are responsible for performing these procedures then testing the engines before they are approved for return to service.”
An Ultrasonic Cleaner Removes Tough Carbon Deposits
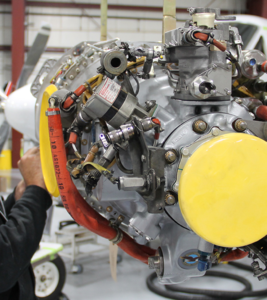
Baked-on carbon deposits are particularly difficult to remove. “Mechanical methods such as soaking, brushing or using steel wool in solvents are not only time consuming; they risk damage to precisely fabricated, highly machined fuel nozzle surfaces,” Scott points out. “Moreover, no mechanical cleaning procedures have the ability to reach into tiny internal fuel nozzle orifices where contaminants may deposit.”
Instead Elliott Aviation uses a process involving ultrasonic cleaning to restore jet engine fuel nozzle assemblies to a like-new condition. The procedure incorporates a 2.5-gallon capacity tabletop Elma E100H ultrasonic cleaner obtained from Tovatech, operating at 37 kHz and equipped with a heater, timer and drain.
“Ultrasonic cleaning involves the implosion of billions of microscopic bubbles against surfaces being cleaned,” Scott explains. “Bubbles are created by generator powered ultrasonic transducers bonded to the bottom of the tank containing the cleaning solution. As bubbles violently implode they blast and carry away the most tenacious of deposits but without damaging the highly machined surfaces.
“Because the bubbles are so small,” Scott continues, “they are able to penetrate interior surfaces of the nozzles – areas impossible to reach by any other cleaning method. The Elma unit is also equipped with what is called a continuous ‘sweep’ mode that evenly distributes cleaning action throughout the cleaning solution to avoid areas of overly intense and lack of cavitation action.”
Another advantage using ultrasonic cleaning is that personnel avoid contact with cleaning solution chemistries that may be employed with manual cleaning processes.
Jet Engine Maintenance with Ultrasonic Cleaning
Disassembly and part preparation procedures follow the P&W Maintenance Manual. Fuel nozzle assembly units are positioned in a mesh basket sized to fit inside the Elma E100H ultrasonic cleaner.
“For cleaning we use Ardrox 185L, recommended for removing tenacious deposits of carbon,” Scott says. “The recommended dilution is 24 to 30% with water. The recommended cleaning temperature is 90⁰C and the cleaning cycle approximately 1 hour.”
Before cleaning begins the solution is prepared. General procedures call for filling the tank half way with water, adding the required amount of Ardrox then adding water to the fill line. Experience will help to determine liquid displacement by parts being cleaned. The best cleaning results are achieved when the solution is at the fill line.
Activate the ultrasound without a load for about 10 minutes. This drives off trapped air that otherwise inhibits cavitation.
While the highest thermostat temperature setting on the Elma unit is 80⁰C ultrasonic cavitation in itself adds heat allowing the solution to reach the recommended cleaning temperature. The timer allows continuous operation to 12 hours before automatic shut-off.
“At the end of the cleaning cycle, assemblies are thoroughly rinsed in very hot water followed by a secondary rinse in warm water,” Scott says. “A leak and function test is then performed.”
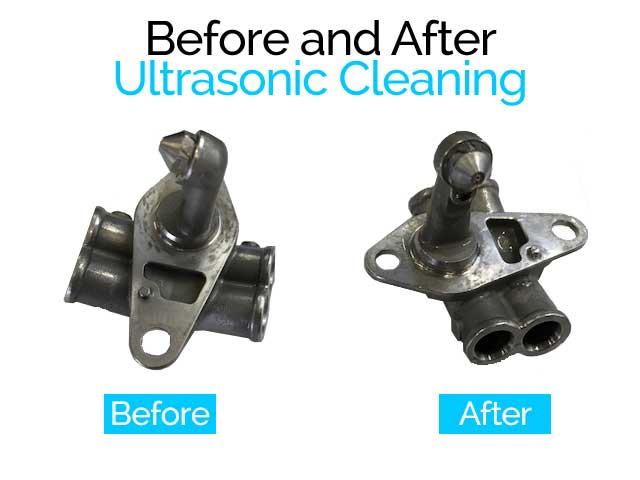
Cleaning Solution Maintenance
As contaminants removed during the cleaning of jet engine fuel nozzle assemblies build up in the solution cleaning efficiency diminishes. Elliott’s operating procedures require replacement after 5 or 6 sets of nozzles have been cleaned. Old solution is disposed of following local regulations. The cleaning tank is rinsed and cleaned following the manufacturer’s operations manual and new cleaning solution is prepared and degassed.
Jet Engine Overhauls
During an engine overhaul, all portions of the engine are disassembled, cleaned, inspected, reassembled, tested and shipped back to the installation agency. The engine consists of four major sections as well as accessories including fuel pumps, fuel nozzles, fuel flow divider, fuel oil heater, constant speed governor, heated tubes and ignition unit.
About Elliott Aviation
Elliott Aviation is a second-generation, family-owned business aviation company offering a complete menu of high quality products and services including aircraft sales, avionics service & installations, aircraft maintenance, accessory repair & overhaul, paint and interior, charter and aircraft management. Serving the business aviation industry nationally and internationally, they have facilities in Moline, IL, Des Moines, IA, and Minneapolis, MN. The company is a member of the Pinnacle Air Network, National Business Aviation Association (NBAA), National Air Transportation Association (NATA), and National Aircraft Resale Association (NARA).
Call or chat with the scientists at Tovatech for information on selecting an ultrasonic cleaner for your critical cleaning requirements.