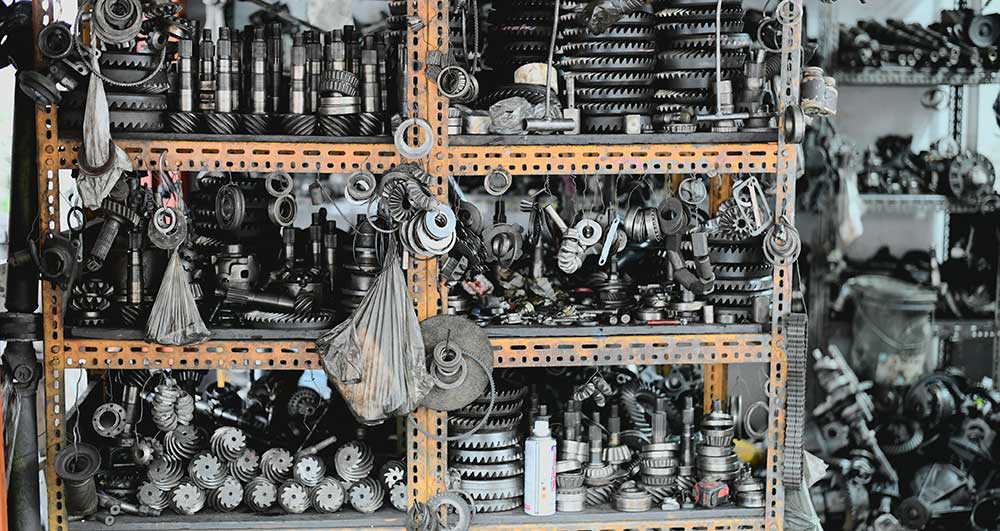
How to Select the Right Parts Washers for Your Needs
In modern manufacturing, repair, and maintenance, achieving impeccable cleanliness of components is not just about aesthetics; it’s fundamental to quality, performance, and longevity. Whether you’re working with precision medical instruments, heavy-duty automotive engine blocks, or delicate electronic components, selecting the appropriate parts washers can make all the difference. This comprehensive guide will walk you through the essential considerations to help you choose the ideal parts washer for your specific application.
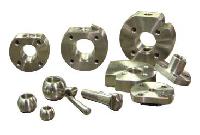
Why Choose a Parts Washer? Beyond Basic Cleaning
The days of manual scrubbing with harsh chemicals are largely behind us. Modern industrial parts washers offer numerous advantages that dramatically improve efficiency, safety, and cleaning consistency:
- Enhanced Efficiency and Throughput: Automated or semi-automated systems significantly reduce the time and labor required for cleaning, allowing personnel to focus on higher-value tasks. You can clean large batches of components simultaneously, drastically increasing your operational throughput.
- Superior Cleaning Consistency: Unlike manual cleaning, which can vary in effectiveness from person to person, a well-chosen parts washer provides repeatable and uniform cleaning results. This consistency is crucial for quality control and meeting stringent industry standards.
- Improved Safety: Parts washers minimize operator exposure to hazardous cleaning chemicals, sharp edges, and hot water. Many systems are designed with enclosed cleaning chambers and automated processes that enhance workplace safety.
- Reduced Labor Costs: By automating the cleaning process, businesses can reallocate labor resources, leading to substantial long-term savings.
- Environmental Compliance: Modern parts washers often incorporate features like filtration, recycling of cleaning solutions, and energy-efficient designs, helping businesses meet environmental regulations and reduce their ecological footprint.
- Optimized Performance & Longevity of Parts: Proper cleaning removes contaminants that can cause premature wear, corrosion, or malfunction, thereby extending the lifespan and performance of your components.
What to Consider When Selecting a Parts Washer
Choosing the right parts washer isn’t a one-size-fits-all decision. A careful evaluation of several key factors will guide you toward the most effective and economical solution.
1. Type and Nature of Contaminants
The type of “soil” or contaminant on your parts is perhaps the most critical factor. Different parts washers excel at removing specific types of residues:
- Oils and Greases: Common in automotive, manufacturing, and heavy machinery. Spray washers and immersion agitation systems with strong detergents are often effective.
- Carbon and Burnt-on Deposits: Frequently found on engine components. Ultrasonic cleaning with specialized solutions or high-pressure spray washing can be necessary.
- Rust and Oxidation: Requires specific rust-removing chemistries, often combined with mechanical action.
- Machining Chips and Fines: Common in metalworking. Spray washers are excellent for flushing away these loose particulates.
- Flux and Solder Pastes: Relevant for electronics manufacturing. Ultrasonic cleaners are often preferred for their ability to reach intricate areas.
- Polishing Compounds/Buffing Rouges: Difficult to remove due to their adhesive nature. Ultrasonics or aggressive spray are usually required.
- Biological Residues: Critical for medical and pharmaceutical applications, requiring specialized disinfectants and validated cleaning processes.
2. Part Material and Geometry
The material your parts are made of and their physical characteristics significantly influence the washer and cleaning chemistry choice:
- Material Compatibility: Aluminum, brass, and other sensitive alloys may react adversely to certain strong alkaline detergents or high temperatures. Steel and cast iron are generally more robust. Plastics may deform under high heat or pressure.
- Intricacy and Geometry: Parts with blind holes, complex internal passages, crevices, or delicate features (e.g., medical instruments, circuit boards) benefit immensely from ultrasonic parts washers due to their ability to clean non-line-of-sight surfaces.
- Size and Weight: Very small parts might require baskets or specialized fixtures. Very large or heavy components might necessitate pass-through conveyor systems or large-capacity cabinet spray washers.
3. Desired Cleanliness Level and Regulatory Compliance
How clean do your parts need to be? The required cleanliness level dictates the rigor of the cleaning process:
- Visually Clean: Free from obvious dirt, grease, or debris.
- Technically Clean: Meets specific standards, such as particulate counts or surface tension tests, often required for painting, coating, or assembly.
- Medical/Sterile Clean: Extremely stringent requirements, often involving multiple cleaning stages, rinsing, and sterilization, adhering to standards like ISO 13485.
- Aerospace Standards: Specific cleaning protocols to prevent foreign object debris (FOD) and ensure material integrity.
Ensure the chosen parts washer and cleaning process can consistently achieve and, if necessary, validate these cleanliness levels.
4. Throughput Requirements
Consider your production volume and the speed at which parts need to be cleaned:
- Batch Cleaning: For lower volumes or varied parts, a batch-style washer (e.g., cabinet spray washer, tabletop ultrasonic unit) where parts are loaded and processed in cycles might suffice.
- Continuous Cleaning: High-volume production lines often benefit from conveyorized parts washers (spray or ultrasonic) that allow for continuous loading and unloading, integrating seamlessly into automated workflows.
- Cycle Time: Evaluate how long each cleaning cycle takes and if it aligns with your overall production schedule.
5. Budget and Operational Costs
While the initial purchase price is important, consider the total cost of ownership:
- Purchase Price: Varies widely based on size, technology, features, and automation level.
- Operational Costs: Include water consumption, energy usage (heating, pumps), chemical consumption, waste disposal, and labor.
- Maintenance: Consider routine maintenance, filter replacement, and potential spare parts.
- Return on Investment (ROI): How quickly will the efficiency gains and quality improvements justify the investment?
6. Utility Requirements
Ensure your facility can support the washer’s needs:
- Power: Voltage, amperage, and phase requirements.
- Water: Access to clean water, pressure, and flow rate. Consider if deionized (DI) water is necessary for rinsing.
- Drainage: Adequate floor drains and waste disposal systems for spent cleaning solutions.
- Ventilation: For systems using volatile chemicals or producing significant steam.
- Compressed Air: Some systems may require compressed air for drying or atomizing sprays.
Types of Parts Washers: An In-Depth Look
Understanding the different types of parts washers is crucial for making an informed decision.
1. Ultrasonic Parts Washers
- How they work: Ultrasonic cleaners use high-frequency sound waves (typically 20 kHz to 200 kHz) to create microscopic bubbles (cavitation) in a liquid. These bubbles rapidly collapse, generating powerful implosions that dislodge contaminants from all surfaces, including intricate crevices and blind holes.
- Ideal for: Delicate parts, components with complex geometries, small parts, parts requiring extremely high cleanliness (e.g., medical instruments, jewelry, electronics, fuel injectors, carburettors).
- Benefits: Highly effective on intricate parts, gentle on surfaces, excellent for precision cleaning.
- Considerations: Can be slower for very large batches of simple parts, requires specialized cleaning solutions.
2. Spray Parts Washers
- How they work: These washers use high-pressure jets of heated water and detergent to blast away contaminants. Parts are typically placed on a rotating turntable or conveyor belt within an enclosed cabinet.
- Ideal for: Larger parts, parts with relatively simple geometries, heavy grease and oil removal, automotive parts (engine blocks, transmission housings), industrial components.
- Types:
- Cabinet Spray Washers: Common for batch cleaning, with parts loaded into a front-opening or top-loading cabinet.
- Conveyorized Spray Washers: Used for continuous high-volume cleaning, where parts move along a conveyor through multiple cleaning and rinsing stages.
- Benefits: Fast, powerful cleaning, good for heavy-duty applications, efficient for large parts.
- Considerations: Less effective on intricate internal passages, can be noisy, consumes more energy for heating water.
3. Immersion / Agitation Parts Washers
- How they work: Parts are submerged in a heated cleaning solution and then agitated (mechanically moved up and down) to create a scrubbing action that dislodges contaminants.
- Ideal for: Parts with moderate complexity, batch cleaning, pre-cleaning for other processes, general industrial maintenance.
- Benefits: Simple to operate, good for soaking stubborn grime, often uses aqueous (water-based) solutions.
- Considerations: Slower than spray or ultrasonic for some applications, may not achieve the highest levels of cleanliness on highly intricate parts.
4. Vapor Degreasers (Historical Context)
- How they work: Used solvent vapors to clean parts. While highly effective, environmental regulations have significantly restricted their use due to ozone depletion and other concerns.
- Note: Modern alternatives like advanced aqueous or ultrasonic systems have largely replaced traditional vapor degreasers for most applications.
Operational Considerations and Maintenance
Once you’ve chosen your parts washer, proper operation and maintenance are key to maximizing its performance and lifespan.
- Cleaning Solutions: Always use detergents or solvents specifically designed for your parts washer type and the contaminants you’re removing. Pay attention to concentration, temperature, and pH levels for optimal results.
- Water Quality: Hard water can leave mineral deposits. Consider deionized (DI) or reverse osmosis (RO) water for final rinses, especially for high-purity applications.
- Filtration: Regularly clean or replace filters to remove suspended solids, extending the life of your cleaning solution and preventing re-deposition of contaminants.
- Drying Methods:
- Air Drying: Simple, but can leave water spots.
- Hot Air Blowers: Accelerate drying and reduce spotting.
- Vacuum Drying: Ideal for parts with complex geometries, ensuring complete drying without water marks.
- Routine Maintenance: Follow the manufacturer’s guidelines for cleaning tanks, checking pumps, inspecting nozzles (for spray washers), and servicing ultrasonic transducers (for ultrasonic units). Proactive maintenance prevents costly downtime.
Future Trends in Parts Washing
The field of industrial cleaning is continually evolving, driven by demands for greater efficiency, sustainability, and integration:
- Automation and Robotics: Increasing integration of robotic loading/unloading, automated transfer systems, and fully integrated cleaning cells within production lines.
- Sustainability: Focus on closed-loop systems for water and chemistry recycling, energy-efficient designs (e.g., improved insulation, heat recovery), and the development of biodegradable and eco-friendly cleaning agents.
- Smart Cleaning Systems (Industry 4.0): Integration of IoT sensors for monitoring solution parameters (temperature, concentration, contamination levels), predictive maintenance alerts, and data analytics to optimize cleaning processes and reduce operational costs.
Why Invest in Researching the Right Parts Washer
Selecting the right parts washer is a strategic investment that impacts your product quality, operational efficiency, and bottom line. By carefully evaluating the type of contaminants, part material and geometry, desired cleanliness levels, throughput requirements, and long-term costs, you can make an informed decision. Tovatech offers a wide range of industrial, ultrasonic, and spray parts washers, along with expert guidance, to help you find the perfect cleaning solution for your unique needs. Contact us today to discuss your application and ensure your components are impeccably clean, every time.