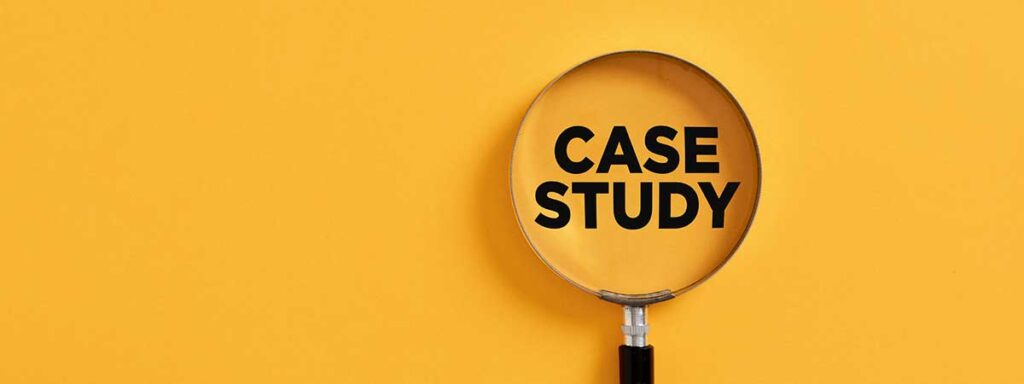
Case Study: Solvent Ultrasonic Cleaning Helps Porvair Filtration
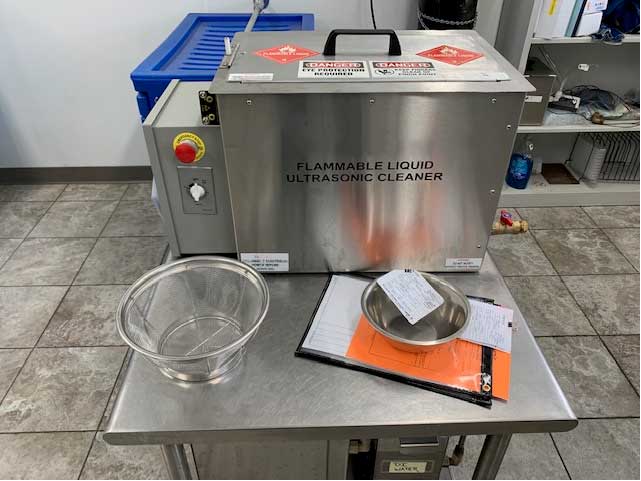
The following is a Case Study about how Porvair Filtration is using an ultrasonic cleaning system successfully in their cleaning processes.
An explosion-proof ultrasonic cleaning system satisfies customers’ preferences for flammable solvents employed during initial cleaning processes for new and reconditioned stainless-steel filters, reports Jeff Bernier, Quality Manager at Porvair Filtration Group in Caribou, ME.
“Solvent ultrasonic cleaning falls into our passivation cycle as a means of improving the corrosion resistance of our 316L stainless steel filters by removing ferrous contaminants like free iron from surfaces, and restoring them to their original corrosion specifications,” Mr. Bernier explains, adding “many of our chromatography customers expect it.”
Solvent Ultrasonic Cleaning Replaces Aqueous Solutions for Porvair Filtration
“Our explosion-proof ultrasonic cleaner allows us to safely use flammable solvents versus previously employed non-flammable aqueous solutions for initial cleaning,” Mr. Bernier says.
“Grade A isopropanol alcohol and pharmaceutical grade acetone are the preferred solvents. However, they require specially designed ultrasonic cleaners as well as compliance with strict safety standards.
“These include the National Electric Code (NEC), National Fire Protection Association (NFPA), our plant safety personnel and local fire regulations.
“Meeting these requirements led us to investigate and procure a 9-gallon capacity SOL XP explosion proof ultrasonic cleaner from Tovatech,” he says.
Jeff Bernier, Porvair Filtration
The SOL XP explosion-proof unit operates at 40 kHz ultrasonic frequency, complies with all Class I, Division 1 (CID1) code and zone requirements, and carries an Intertek ETL Certification.
It is shipped with a remote electrical panel to be located outside the CID1 envelope. The tank is equipped with intrinsically safe circuits and the transducer enclosure is nitrogen inerted for additional fire protection.
Porvair Filtration’s Ultrasonic Cleaning Cycle
“Our solvent ultrasonic cleaning cycle is pretty simple,” Jeff says. “We place the customer’s parts into a basket strainer, lower the basket into the solvent, close the lid, set the timer for 15 minutes and walk away to attend to other tasks.
“Once the cycle is complete, we lift the basket out of the tank, allow the solvent to run back into the tank and then place the parts on a stainless-steel sheet. From there, the sheets are placed into an explosion proof dryer.”
Porvair Filtration Uses Safe Ultrasonic Cleaning with Volatile Solvents
As a general rule, whenever you install an explosion-proof ultrasonic cleaner such as the SOL XP for use with volatile solvents you must check with local public safety officials and your plant safety personnel to ensure compliance.
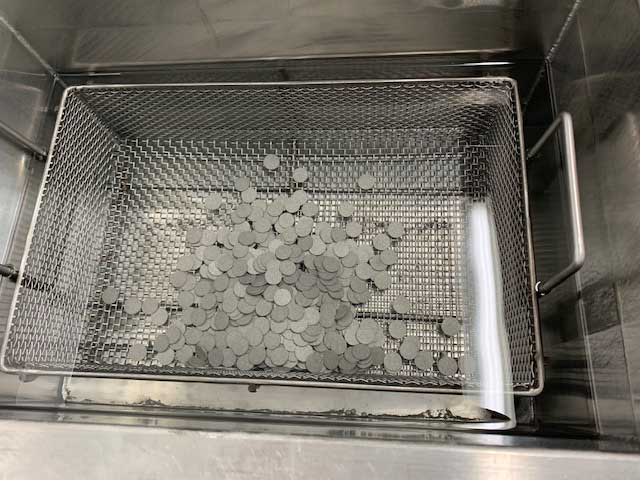
Here are some suggestions that help to meet regulations:
- Be sure that solvent vapor cannot come in contact with a potential source of a spark.
- A suitable exhaust system should be positioned over the ultrasonic cleaner to draw off fumes and protect personnel from inhaling them.
- Check the tank and enclosure for damage that could result in leakage.
- Follow instructions to maintain proper solvent level in the tank. This is particularly critical when cleaning with volatile solvents.
- No personal electronics should be used in proximity to the cleaners.
More stringent regulations may apply depending on the flammable liquid ultrasonic cleaner you select as well as where and how they are employed.
For more useful information on this important topic check our blog post on the ultimate source for ultrasonic cleaning with flammable solvents.
Then feel free to contact the Tovatech scientists for expert advice on selecting the correct unit for your operations and information on code compliance.
About Porvair Filtration Group
Porvair Filtration Group operates five design and manufacturing sites producing filters and sensor protectors used in applications including analytical and process instruments, media retention for gas drying and purification, frits for chromatography, flame arrestors for combustible gas monitoring and flow restrictors for gas flow control devices.