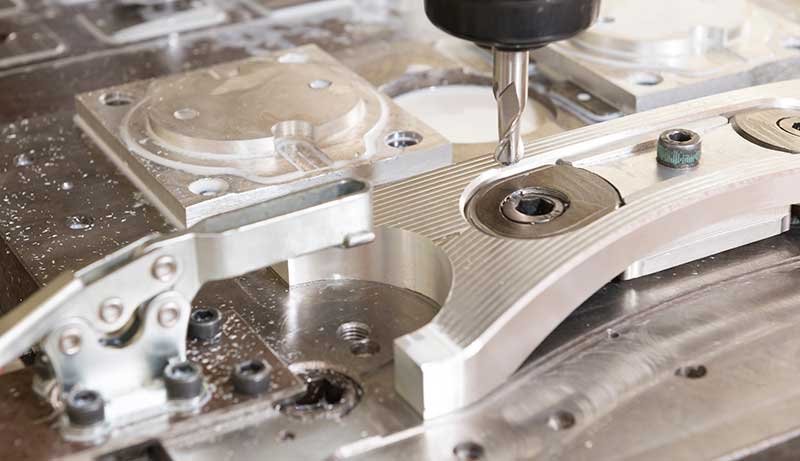
How To Efficiently Clean Machined Parts
Whether you’re running a CNC shop, fabricating components for aerospace, or maintaining equipment on the production line, clean machined parts are essential for performance, durability, and downstream processes like coating or assembly. Contaminants such as cutting fluids, metal fines, and oxidation not only affect part quality — they can also lead to failed inspections and costly rework.
Industrial manufacturers have several cleaning options at their disposal. In this post, we’ll walk through three of the most effective methods for cleaning machined parts, with a focus on ultrasonic cleaning — a highly efficient solution for precision results. We’ll also compare it to other common methods so you can make the best choice for your facility.
Why Cleaning Machined Parts Is Critical
Before we dive into methods, let’s talk about why cleanliness matters. Machining operations leave behind a mix of contaminants:
- Coolants and lubricants
- Metal chips and fines
- Oxidation or corrosion products
- Dust, dirt, or polishing residues
Leaving these residues in place can lead to poor fit during assembly, impaired surface treatments (like plating or painting), and even premature component failure. Cleanliness is often a specification requirement in aerospace, automotive, and medical manufacturing.
That’s why finding the right method to clean machined parts is a critical part of your workflow — not an afterthought.
1. Ultrasonic Cleaning: The Fast, Thorough Solution for Precision Parts
For many industrial operations, ultrasonic cleaning is the go-to solution — and for good reason. It’s fast, thorough, and can clean complex geometries that brushes or sprays can’t reach.
How It Works
Ultrasonic cleaners use high-frequency sound waves (usually in the 25–80 kHz range) transmitted through a cleaning solution. These sound waves create microscopic bubbles in a process called cavitation. When the bubbles collapse, they generate intense localized pressure and temperature — dislodging contaminants from the surface and even from blind holes, threads, and internal channels.
Key Benefits
- Deep, uniform cleaning of parts with intricate geometries
- Non-damaging, ideal for delicate or tight-tolerance components
- Can be used with aqueous or solvent-based solutions
- Reduces the need for manual scrubbing or multi-step processes
- Fast cycle times (often under 15 minutes)
Best Applications
Ultrasonic cleaning is especially useful for:
- Fuel injectors, valves, and aerospace components
- Medical or dental instruments
- Parts with fine threads, small holes, or complex internal passages
- Precision assemblies prior to coating or bonding
If you’re dealing with parts that demand spotless surfaces and a non-abrasive process, ultrasonic cleaning delivers consistent, repeatable results.
We often speak with customers using solvents to remove oil and grease from metal parts. They don’t realize that water-based formulations have been improved to the extent that solvent cleaning is no longer necessary. There are significant advantages to switching to ultrasonic cleaning with water-based soaps instead of manual cleaning with toxic, flammable solvents.
2. Aqueous Parts Washing: A Reliable Workhorse
Another popular option for cleaning machined parts is aqueous parts washing — typically using a water-based cleaning solution combined with agitation, heat, and sometimes spraying.
How It Works
Parts washers come in various configurations: manual spray cabinets, automated conveyor systems, and immersion tanks with agitation or rotating baskets. Most systems use a heated alkaline detergent to break down oils, greases, and particulates.
Pros and Cons
✅ Cost-effective and easy to operate
✅ Suitable for larger parts or high-throughput needs
✅ Available in automated formats for production lines
❌ May struggle with tight geometries or blind holes
❌ Not as effective for fine or delicate components
❌ Requires drying cycle and regular solution maintenance
Best Applications
Aqueous parts washing is ideal for general-purpose cleaning of:
- Castings and housings
- Brackets, gears, or frames
- Heavily soiled or oily components
If you’re cleaning bulky or rugged parts with less concern about fine detail, this method is often sufficient — and budget-friendly.
3. Solvent Cleaning: Targeted Use for Stubborn Contaminants
Solvent cleaning has been used for decades to remove grease, oils, and certain residues that water-based systems can’t dissolve. While it’s less common today due to environmental and safety concerns, solvent cleaning still plays a role in specific use cases.
Applications that require solvent-based cleaning are often government regulated processes that specify the use of solvents. For example, if the FDA approved a process to clean a medical device with solvent, it’s very difficult and time consuming to change that approved process. Although a customer may be aware that switching to a water-based process would be safer and easier, it’s just too much trouble to make the change.
How It Works
Parts are either wiped, immersed, or sprayed with a chemical solvent designed to dissolve specific contaminants. In some facilities, vapor degreasing units are used to apply and recycle solvent vapors in a controlled environment.
Pros and Cons
✅ Effective for hydrocarbon-based residues
✅ Can clean without water exposure (important for sensitive parts)
✅ Often used as a pre-treatment for coatings
❌ Health, safety, and environmental concerns
❌ Requires proper ventilation and PPE
❌ Solvent disposal must meet regulatory standards
Best Applications
Solvent cleaning is typically reserved for:
- Parts with coatings or oxidation that require chemical stripping
- Small batches where water use is impractical
- Pre-cleaning before plating or painting
Solvent cleaning can be highly effective — but it’s best used selectively and with full awareness of safety protocols.
Choosing the Right Method to Clean Machined Parts
When evaluating cleaning methods, it’s important to match the process to the part requirements, contaminants, and throughput needs. Here’s a quick comparison:
Method | Best For | Not Ideal For |
---|---|---|
Ultrasonic | Small, complex, precision parts | Extremely large parts |
Aqueous Washers | General-purpose and large parts | Very fine or intricate features |
Solvent Cleaning | Heavy oils, selective stripping | High-volume or eco-sensitive ops |
In many industrial settings, these methods are even used in combination — for example, pre-washing in an aqueous spray system followed by a final ultrasonic clean.
Final Thoughts
No matter your industry, ensuring clean machined parts is essential to performance, product quality, and compliance. While there’s no one-size-fits-all solution, ultrasonic cleaning stands out for its ability to remove microscopic contaminants from even the most complex parts — safely and efficiently.
If you’re unsure which system is best for your application, the experts at Tovatech are here to help. Whether you need help selecting an ultrasonic cleaner or designing a complete cleaning workflow, give us a call or start a chat — we’re ready to guide you to the right solution.