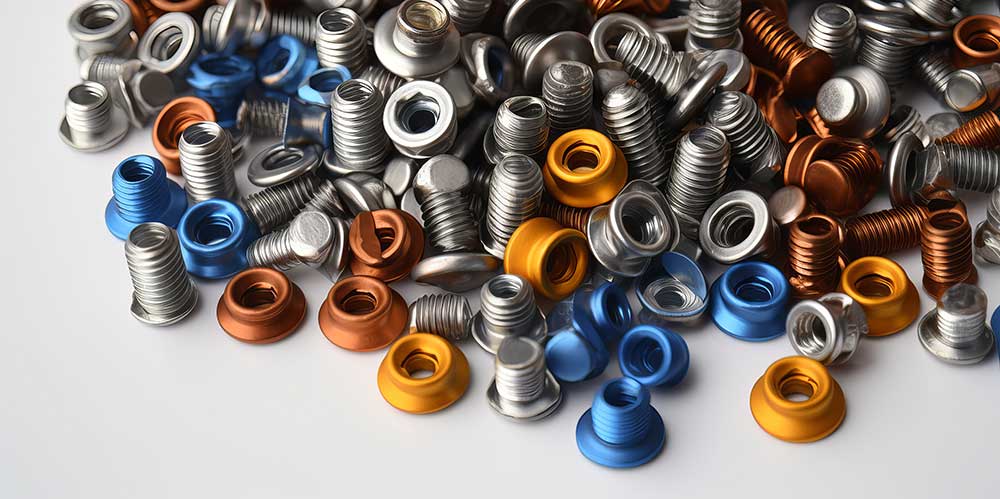
Streamline Inventory Management with a Counting Scale
Efficient inventory management is crucial for businesses across various industries. When dealing with large quantities of small or lightweight items, accurate counting is essential for maintaining inventory control, ensuring accurate billing, and optimizing production processes. A counting scale can provide a reliable and efficient solution for streamlining these tasks, offering precision and speed for high-volume counting operations.
The Power of a Counting Scale
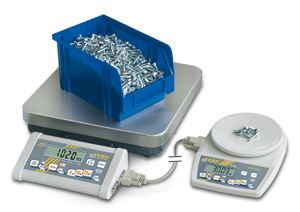
Counting scales combine the functionality of a precision balance with advanced counting algorithms to accurately determine the quantity of items based on their weight. This eliminates the need for manual counting, saving time and labor costs while minimizing errors. By using a precision reference scale with a platform scale, you achieve a high degree of accuracy, even when individual pieces weigh very little. This system allows personnel to count very low weight items in very large numbers and quickly switch between counting different products.
Key Benefits of Counting Scales
- Increased Accuracy: Counting scales eliminate human error associated with manual counting, ensuring precise and reliable counts.
- Improved Efficiency: Counting scales significantly speed up the counting process, freeing up valuable time and resources.
- Inventory Control: Accurate counts contribute to better inventory management, reducing stockouts and overstock situations.
- Cost Savings: By minimizing counting errors and optimizing inventory, businesses can reduce costs associated with waste, overproduction, and inaccurate billing.
- Streamlined Operations: Counting scales streamline packaging and shipping processes, improving overall operational efficiency.
How Counting Scales Work
Counting scales typically utilize a two-step process:
- Reference Counting: A known quantity of items is placed on the reference scale to establish a reference weight. This data is then stored in the scale’s memory.
- Bulk Counting: The bulk quantity of items is placed on the platform scale. The digital scale calculates the total count based on the reference weight and the total weight of the items.
Choosing the Right Counting Scale
Selecting the appropriate counting scale depends on several factors:
- Capacity and Readability: Determine the maximum weight and the required counting accuracy for your application. Counting scales are available in various capacities, with readouts suitable for different levels of precision.
- Item Size and Weight: Consider the size and weight of the items you will be counting. Some scales are specifically designed for very small or lightweight items.
- Counting Speed: If high-speed counting is critical for your operation, look for digital scales with fast processing capabilities.
- Connectivity and Features: Consider features like data logging, connectivity to external devices (printers, computers), and built-in software for enhanced functionality.
- Environmental Conditions: If the scale will be used in a harsh environment, choose a model with appropriate protection ratings (e.g., dust and water resistance).
Calibration and Care of a Counting Scale
Regular calibration is essential for maintaining the accuracy of your counting scale. Establish a standard operating procedure for periodic recalibration using external calibration weights. Protect the scale from temperature extremes, unnecessary movement, and vibrations to ensure consistent performance.
Optimizing Your Counting Processes
Counting scales are valuable tools for businesses that handle large quantities of small items. By automating the counting process, these digital scales improve accuracy, efficiency, and inventory control, ultimately contributing to cost savings and streamlined operations.
Call or chat with our weighing equipment specialists to determine the most suitable counting scale for your specific needs and applications.