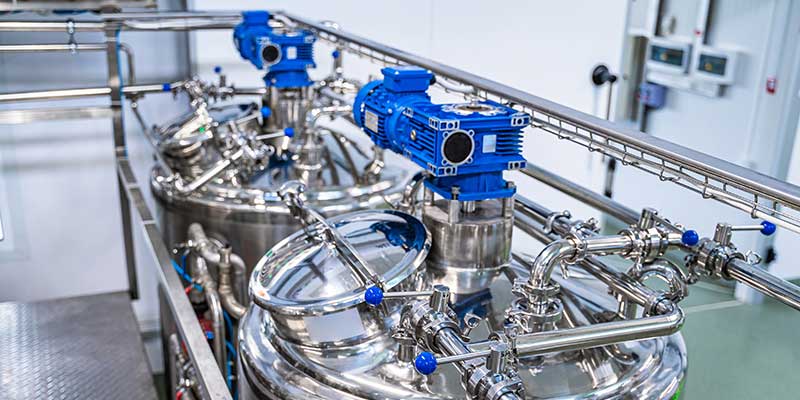
IQ, OQ, PQ Examples for Analytical Instruments
Analytical instruments confirm processing equipment used in the pharmaceutical, food and other industries meet standards set by the FDA, the Code of Federal Regulations Title 21 and other regulatory bodies. Standards apply from the very beginning with design qualification. At the customer location equipment is validated and verified via initial and ongoing tests described in this post as IQ, OQ, PQ examples.
IQ, OQ, PQ Examples Defined
In brief IQ, OQ and PQ mean Installation Qualification, Operational Qualification and Performance (or Process) Qualification . An example is an HPLC system, including its pumps. These systems must precisely and accurately analyze pharmaceutical compounds as they proceed from R&D into manufacturing. We’ll go into that in more detail later.
But first, some more detail on our IQ, OQ, PQ Examples
Installation Qualification Described
As described in an FDA Group blog post “Newly installed or modified equipment must first be validated to determine if it’s capable of producing the desired results.”
But this IQ example is not a one-time step for brand new equipment. It also applies to used equipment that you purchase for your site. Moreover, IQ can also come into play if your equipment is moved to another location in your facility.
Successful passing the IQ hurdle is aided by adhering to manufacturers’ guidelines during the installation procedures. These can be quite extensive and include issues such as floor space, adequate power and the operating environment.
Operational Qualification Defined
Once the equipment is installed and passes the IQ hurdle it must be qualified to operate “as advertised” under actual operating conditions expected by the user and within specifications provided by the manufacturer.
Think of the OQ example as a test run.
As described by our above cited source, “In general, OQ serves as a detailed review of hardware or software startup, operation, maintenance, cleaning and safety procedures (if and where they’re applicable). Every unit of hardware and software must be shown to be operating within the specified limits.”
OQ as well as our IQ examples can be performed by properly trained onsite personnel or by engaging qualified outside service providers.
As an OQ example, tests for an HPLC system include checking the accuracy and precision of the pump flow. As noted above you’ll find a brief description of this exercise at the end of this post.
Performance Qualification Described
As a PQ example, performance qualification must be successfully achieved before starting commercial production.
Performance qualification (or Validation) means that your equipment, under actual operating conditions, meets all predetermined requirements.
If several pieces of equipment are involved, all must work together “as advertised” before a PQ certificate is issued.
A detailed look at process validation is found in this FDA publication. And please keep in mind that PQ as with OQ is not a one-time exercise but part of an ongoing program to help assure that your company conforms to good manufacturing practices.
An IQ, OQ, PQ Example:
Validating High Performance Liquid Chromatography Systems
Researchers know a critical if not the most critical aspect of a High Performance Liquid Chromatography (HPLC) system is providing uniform and reproducible column retention times for analytes. The retention time is dependent upon the pump flow rate. Therefore, the test protocols include testing the pump flow for accuracy and precision.
Digital HPLC flowmeters such as the FlowCal 5000 are used to measure the accuracy of HPLC pumping systems in order to meet FDA and other regulations regarding IQ, OQ and PQ of equipment used in the pharmaceutical and biopharmaceutical industries as well as other analytical labs.
The process demands accurate, reproducible column retention time as an analyte (what is being analyzed) is pumped through the HPLC system.
After initial IQ and OQ qualification , periodic calibration (PQ) checks of HPLC pump systems must be undertaken to confirm OQ and to identify and correct flow rate variances that may develop, for example, from factors such as worn pump seals or sediments that interfere with flow rates.
These calibration tests are performed by checking flow rates while pumping solvent through the HPLC system.
Testing the flow rate manually is a long and tedious process as described in our post on flow meter accuracy.
Instead, on-site personnel or those engaged from outside service providers can couple a FlowCal 5000 digital HPLC flowmeter to collect solvent exiting from the HPLC system.
Then the FlowCal 5000 takes over and makes repeated flow rate measurements that are sent via an RS232 interface to a printer or computer for record keeping. The researcher is free to do other work in the lab.
The benefits of the FlowCal 5000 are expressed in several user testimonials found at the bottom of the FlowCal 5000 page linked above.
IQ, OQ, PQ Examples Documentation
Record keeping is critical when dealing with government and other agencies involved in food and pharmaceutical processing. As noted in our links above the FlowCal 5000 is supplied with documentation regarding its performance capabilities.
But like all precision instrumentation, the digital HPLC flowmeter should re recalibrated annually to insure accurate performance.
Need More Info? For additional information on IQ, OQ, PQ examples and issues, or for further details on the FlowCal 5000 liquid flow meter please contact the scientists at Tovatech.