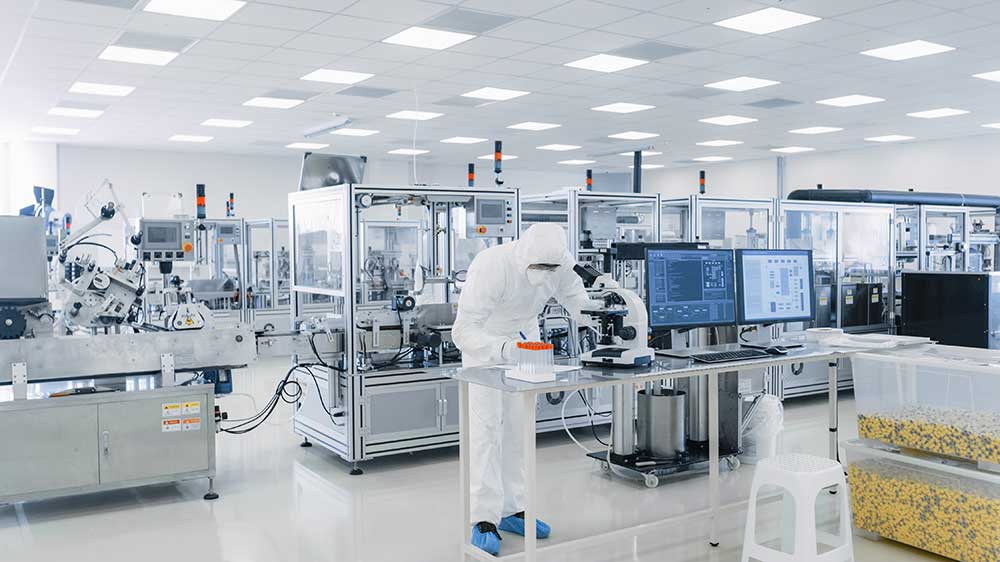
Ensuring Drug Safety and Efficacy: The Critical Role of Stability Chambers in Pharmaceutical Development
Stability testing is a cornerstone of pharmaceutical development, ensuring the safety, efficacy, and quality of drugs and medicinal products throughout their lifecycle. As defined by the FDA, these tests provide crucial evidence of how environmental factors like light, humidity, and temperature, as well as time, affect a drug’s characteristics. This data is used to establish re-test periods for drug substances, define shelf life for medicinal products, and determine recommended storage conditions. Central to this process are stability chambers, specialized equipment designed to meticulously control environmental parameters.
Why are Stability Chambers Essential?
Stability chambers are indispensable tools in pharmaceutical research and manufacturing. They provide a controlled environment for conducting stability studies, which are mandated by regulatory bodies like the FDA (21 CFR Part 211 Section 166). These studies are not merely a formality; they are essential for:
- Determining Shelf Life: Stability testing reveals how long a drug product maintains its desired quality and potency under specific storage conditions. This information is critical for establishing expiration dates and ensuring patient safety.
- Identifying Degradation Pathways: By exposing drug samples to various environmental stresses, stability studies help identify potential degradation pathways and understand how the drug’s chemical structure might change over time. This knowledge is crucial for formulation development and optimization.
- Optimizing Packaging: The type of packaging used can significantly impact a drug’s stability. Stability chambers allow researchers to evaluate different packaging materials and their ability to protect the drug from environmental factors.
- Meeting Regulatory Requirements: Regulatory agencies worldwide require comprehensive stability data before approving new drugs. Stability chambers are essential for generating the necessary data to meet these stringent requirements.
The Stability Testing Process: More Than Just a Chamber
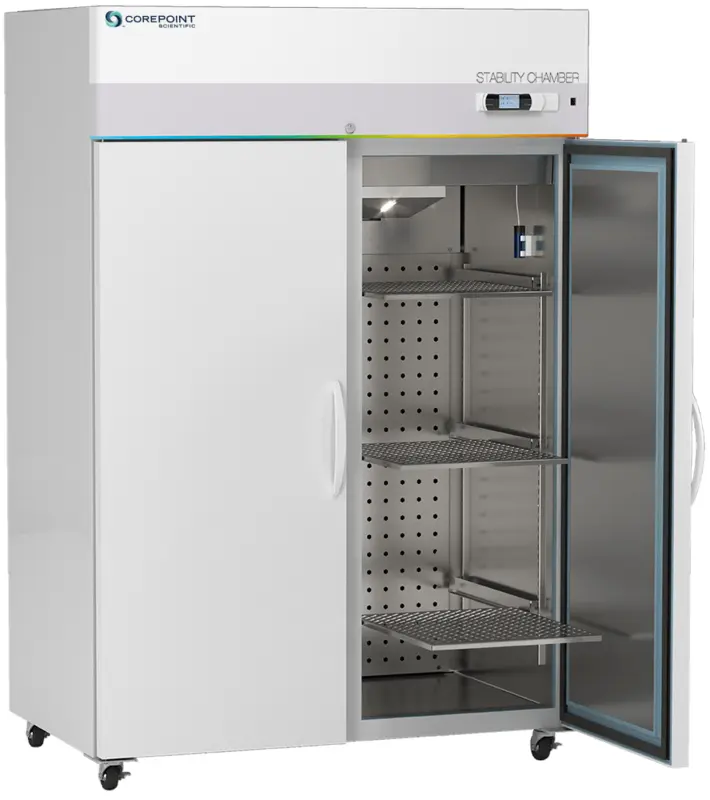
While stability chambers provide the controlled environment, successful stability testing involves a well-defined and meticulously executed program. It’s not simply a matter of “plugging in” a chamber. A robust Stability Test Program, documented in a standard operating procedure (SOP) and approved by all relevant personnel, is critical. This program addresses crucial aspects, including:
- Sample Preparation and Handling: Detailed procedures for preparing and handling drug samples are essential to ensure consistency and prevent contamination.
- Testing Conditions: Specific temperature and humidity conditions, as outlined in ICH guidelines, are meticulously maintained within the stability chamber.
- Data Collection and Analysis: Regular monitoring and analysis of drug samples are conducted to track changes in their physical, chemical, and microbiological properties.
- Deviation Management: The SOP must outline procedures for handling deviations from established parameters, such as out-of-spec humidity or temperature fluctuations. This includes investigating the cause of the deviation, assessing its impact on the study, and implementing corrective actions.
Qualification and Maintenance: Ensuring Chamber Reliability
Before a stability chamber can be used for testing, it must undergo a rigorous qualification process, consisting of three stages:
- Installation Qualification (IQ): Verifies that the chamber is installed correctly and according to manufacturer specifications.
- Operational Qualification (OQ): Demonstrates that the chamber operates within specified parameters and meets pre-defined performance criteria.
- Performance Qualification (PQ): Confirms that the chamber consistently performs as intended under actual testing conditions.
These qualifications are typically performed by metrology or validation personnel using calibrated equipment. Detailed records of the qualification process are maintained by the Quality Assurance department. Furthermore, ongoing performance maintenance and verification tests are essential to ensure the chamber’s continued reliability and accuracy.
Modern Stability Chambers: Advanced Technology for Precise Control
Modern stability chambers, like the lines offered by Tovatech, are equipped with sophisticated technology to ensure precise environmental control and data integrity. Key features include:
- Programmable Microprocessor Controls: Allow for precise setting and control of temperature, humidity, and other environmental parameters.
- LCD Control Panel and Message Center: Provide real-time monitoring of chamber conditions and display any alarms or error messages.
- Comprehensive Monitoring and Alarm Systems: Continuously monitor critical functions and trigger alarms in case of out-of-spec conditions, door ajar situations, power failures, or other anomalies.
- Data Logging and Traceability: Events are date and time stamped and logged in nonvolatile flash memory, ensuring accurate record-keeping and traceability. This data is crucial for audits and regulatory submissions.
Choosing the Right Stability Chamber:
Selecting the appropriate stability chamber is a crucial decision. Factors to consider include:
- Capacity: The size of the chamber should be adequate to accommodate the expected volume of samples.
- Temperature and Humidity Range: The chamber must be capable of achieving the specific temperature and humidity conditions required for the intended studies.
- Control System: A reliable and user-friendly control system is essential for accurate and consistent performance.
- Features: Consider features such as data logging, alarm systems, and remote monitoring capabilities.
- Manufacturer Reputation and Support: Choose a reputable manufacturer that offers reliable products and excellent customer support.
Questions? No Problem. Contact Our Experts for Help.
Stability chambers are indispensable tools in the pharmaceutical industry, playing a critical role in ensuring the safety, efficacy, and quality of medications. By providing a controlled environment for stability testing, these chambers enable researchers and manufacturers to gather crucial data, meet regulatory requirements, and ultimately protect patient health. The selection, qualification, and maintenance of stability chambers are critical aspects of a robust stability testing program, contributing to the development of safe and effective pharmaceutical products.