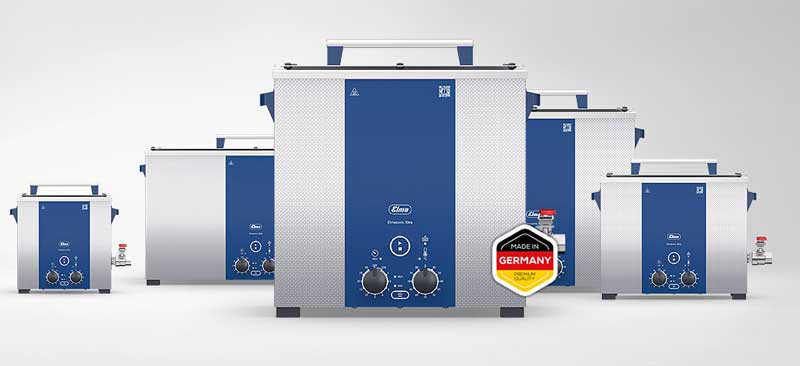
Choosing the Right Industrial Ultrasonic Cleaner Features and Options
Industrial ultrasonic cleaners can represent a sizeable investment. Here we define these units, what to look for when purchasing, and offer equipment options to help you make the right selection. Included are examples of industrial ultrasonic cleaner applications.
Industrial Ultrasonic Cleaner Defined
Industrial ultrasonic cleaners are heavy-duty cleaning systems designed for continuous operation and the effective removal of contaminants from large or numerous parts. The job to be done – not the size of the cleaner or items being cleaned – defines these products.
That’s why industrial units are available in benchtop and floor mounted configurations.
Heavy-duty ultrasonic parts washing usually means long-term (multi-hour) continuous cleaning operation. This calls for capabilities such as heavier gauge stainless steel cleaning tanks, automatic time and temperature safety shutoffs, and other features/benefits described here.
Key Industrial Ultrasonic Cleaner Features to Consider
Tank Capacity
Cleaning tanks are specified by dimensions (length, width, depth) and cleaning solution capacity. Key points to consider when selecting tank capacity:
- Parts must be fully immersed in cleaning solutions
- Parts should not contact each other or the tank
- Cleaning baskets, used in most applications, are smaller than tank dimensions
- Dividers and trays offer options for part separation in baskets
Large and/or heavy parts can be suspended in the tank or rest on specially constructed supports on tank bottoms offered on certain industrial units.
Ultrasonic Frequency
Ultrasonic cleaning occurs when billions of microscopic vacuum bubbles implode against surfaces being cleaned to blast loose and carry away contaminants.
- Lower frequencies such as 25 kHz produce larger bubbles. When these bubbles implode they release strong cleaning energy. For removing caked on grease, lapping abrasives or polishing pastes use a low frequency.
- Higher frequencies such as 37, 45 and 80 kHz produce progressively smaller bubbles. These are better for delicate, highly finished parts and those with complex surfaces, blind holes, cracks and crevices.
- Dual-frequency units allow you to broaden service offerings.
For more information please check ultrasonic cleaners and how they work.
Industrial Ultrasonic Cleaner Operating Features
Unit size and operating frequency are two critical specification criteria. Other features that may be important in helping you do the job most efficiently include:
- Temperature controls let you set cleaning solution temperature to the level recommended by the cleaning solution manufacturer.
- Timers control the duration of the cleaning cycle. Some units are designed to start cleaning when the selected temperature is reached and shut down at the end of the cycle.
- Degas mode speeds the removal of trapped air in fresh cleaning solutions. An alternative is allowing the equipment operate for a period of time without a load.
- Sweep provides a slight ± fluctuation in the ultrasonic frequency and serves to even out the cleaning action to avoid “hot spots” or possibly damaging cavitation action, “dead zones” or no cleaning action, and harmonic vibrations that can damage delicate parts such as PCBs.
- Pulse mode boosts ultrasonic power up to 20% to remove stubborn contaminants.
- Dynamic mode optimizes cleaning results by automatically combining the sweep mode for uniform cleaning with the pulse mode that removes stubborn contaminants.
- Eco Mode provides gentle cleaning and a quieter operation, achieving a lower intensity cleaning cycle with sweep frequency.
- Adjustable Power lets you set the cleaning parameters to the job at hand.
Benchtop Industrial Ultrasonic Equipment from Tovatech
Should your parts be heavily contaminated and require long-term cycles a suggestion is a 37 kHz Elmasonic xtra TT unit.
- Operates up to 8 hours a day
- Permanent Sweep mode for uniform cleaning
- Switchable Dynamic mode to increase cleaning intensity
The Elmasonic Xtra series of 37 kHz industrial benchtop ultrasonic cleaners is perfect for production lines, workshops and service bays.
- Extra powerful cleaning mode with consistent, uniform cleaning results
- Energy-saving Eco mode for gentle cleaning of less-soiled parts
- Set bath temperature from 30 to 80⁰C
- Timed cleaning to 30 minutes, continuous to 6 hours
- Welded stainless steel tanks carry a 3-year warranty
Floor-Mounted Mobile Ultrasonic Cleaners from Tovatech
When cleaning a variety of materials consider a dual-frequency ultrasonic cleaner. An example is the Elmasonic X-tra ST line.
- Powerful or gentle dual frequency cleaning 25/45 kHz
- Heavy duty tanks operate to 8 hours a day
- Timer, drain, and heater up to 80° C
- Seven tank sizes from 8 to 67 gallons
- On lockable casters for portability
- In stock for quick delivery
The X-tra ST line offers optional accessories to pre- and post-rinse products and filter cleaning solutions, both contributing to longer cleaning solution effectiveness.
SHIRACLEAN industrial units available in 7 capacities from 25 to 204 gallons are designed for machine shops, equipment maintenance, solder flux removal, printing, electronics, 3-D mold support and a variety of laboratory applications.
- Filtration to prolong solution lifetime
- Weirs and spray bars to remove oils and other floating contaminants
- 40 kHz with Sweep
- Timer, heater, drain
Customized Ultrasonic Cleaners for Industrial Applications
If standard equipment offerings do not satisfy your needs customized units can be constructed to meet your specific requirements. Tovatech scientists are ready to work with you to specify exactly what you need.
- Systems built to your specifications
- Pricing comparable to standard units
- Ideal for parts too large or numerous for off-the-shelf tanks
- High quality equipment with 2-year warranty and excellent technical support
- Optional features available to meet your needs
Ultrasonic Cleaning with Volatile Solvents
Ultrasonic cleaning using volatile solvents such as IPA, acetone and toluene require precautions including meeting local and national regulations to avoid fire and explosions. The SOL XP series of explosion-proof ultrasonic cleaners in 6 tank sizes to 33 gallons help you meet these requirements.
Typical Applications for Industrial Ultrasonic Cleaners
The extent and type of contamination (i.e. dirt, gunk, greases and oils) to be removed may require longer cleaning cycles, pointing to the selection of a heavy-duty ultrasonic cleaner. The following examples provide you with greater detail on when and how these units are used.
- Automotive and power train cleaning and degreasing
- Cleaning costly plastic injection molds to maintain quality output
- Ultrasonic passivation for stainless steel to meet ASTM A967 standards
- Safely remove 3-D printing mold support
- Degreasing heavy parts
- Nondestructive testing of aircraft engine parts
- Cleaning new and reconditioned filters using flammable solvents
Solutions and Frequently Asked Questions
Ultrasonic cleaning solution formulations are available to handle a broad range of cleaning challenges. Selecting the correct formulation can make the difference between OK or perfect results. Check our post on specifying ultrasonic cleaning solutions.
Another useful resource is our answers to ultrasonic cleaner frequently asked questions.
Equipment Investment Considerations & Pricing Guide
Cost-benefit analyses are important to any investment in plant and equipment. When it comes to ultrasonic cleaning industrial parts – or any part for that matter – time saved to achieve desired results is an important consideration.
As a start, download our Pricing Guide offer to get an idea of costs involved.
But before making your final decision we encourage you to call or chat with the scientists at Tovatech. We are ready to help you select the best industrial ultrasonic cleaner for your requirements, whether benchtop or floor mounted.