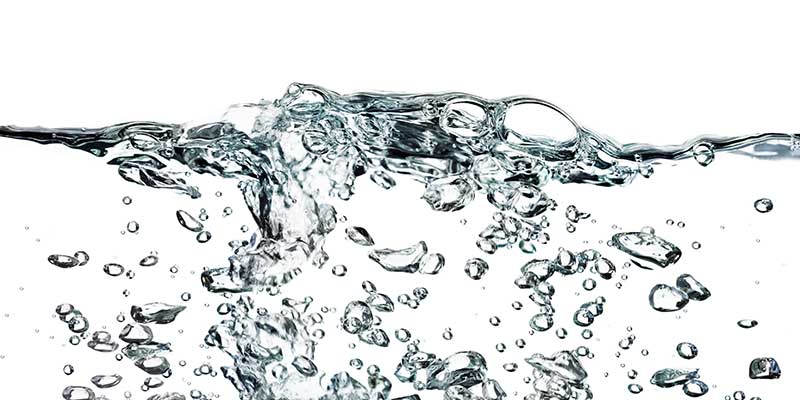
Selecting a Heated Ultrasonic Cleaner
Just as soapy hot water is better than cold for cleaning greasy dishes, pots and pans (and even you!), a heated ultrasonic cleaner solution often “works best” solving tough cleaning challenges. That’s why you should select a heated ultrasonic cleaner to remove deposits of heavy grease, burned on carbon deposits and grime from used engine parts, cutting oils from newly machined components, residues in plastic injection molds, and similarly difficult cleaning challenges.
The Role of a Heated Ultrasonic Cleaner
If you are new to the process of ultrasonic cleaning, we invite you to review our post on how ultrasonic cleaners work. Otherwise, please continue reading about selecting a heated ultrasonic cleaner.
Fast, safe and efficient ultrasonic cleaning cycles call for a judicious blend these variables:
- cleaning solution chemicals
- cleaning solution temperature
- cleaning cycle time
- ultrasonic frequency
Cleaning solution chemicals are selected based on the project at hand in order to provide efficient removal of contaminants. We cover this topic in our post on cleaning solution guidelines.
Cleaning temperature is often recommended by cleaning solution manufacturers. For example, the recommended temperature for the widely used Elma tec clean A4 is 50 – 80⁰C. Ultrasonic cleaners equipped with temperature controls let you set the desired temperature. Some models begin operation when the set temperature is reached.
The time required to achieve efficient cleaning depends largely on the products being cleaned: composition, complexity and nature of contaminants removed. Cleaning time is developed based on experience.
Ultrasonic frequency is discussed later in this post.
How Heat is “Automatically” Created in an Ultrasonic Cleaner
Heater-equipped ultrasonic cleaners speed reaching the desired cleaning solution temperature. But heat is also “automatically” created as well. Here’s why:
Ultrasonic cleaners use generators and transducers that cause the bottom (and sides in some models) of ultrasonic cleaner solution tanks to vibrate as a membrane.
This vibration produces billions of micron-sized vacuum bubbles that implode through a process called cavitation.
The implosion of bubbles against surfaces to be cleaned blasts loose and carries away contaminants far faster and, in most cases safer, than can be achieved by manual cleaning techniques.
Implosions create enormous temperatures on the order of 5,000⁰C. But the bubbles are so small that heat dissipates rapidly. Cleaning solution temperature is relatively unaffected.
Nevertheless, cleaning solution temperature does increase during long cleaning cycles. In fact, during long-term operation cleaning bath temperatures exceeding 60°C (140⁰F) can be reached simply by ultrasonic energy.
This, as well as for other reasons, makes it is unwise to reach into an operating ultrasonic cleaning bath.
Ultrasonic Cleaner Heat: More is Not Always Better
When it comes to a heated ultrasonic cleaner there are two important points to keep in mind. First of all, there’s a limit to when increasing the temperature contributes to the cleaning process. As the cleaning solution temperature increases cavitation action decreases.
That is why heater-equipped ultrasonic cleaners such as the Elma line offered by Tovatech have thermostats with a maximum temperature setting of 80⁰C (176⁰F).
There are, of course, exceptions. Some highly caustic cleaners used for cleaning iron, steel and stainless steel are used at higher temperatures. An example is cleaning jet engine fuel injectors at a temperature of 90⁰C for one hour.
Many heated ultrasonic cleaners are designed to initiate the cavitation process when the set temperature is reached, and provide LED indicators showing the target and actual solutions temperature.
Heated ultrasonic cleaners may be equipped to automatically shut off when solution temperatures get too high.
When Not to Use a Heated Ultrasonic Cleaner
There are certain applications where heat is not necessarily desirable when using an ultrasonic cleaner.
An example is a pre-sterilization or disinfecting step for medical and surgical instruments.
Blood and tissue should be removed from instruments at a temperature below 40⁰C (104⁰F). That’s because elevating the temperature can cause protein in blood to harden and become more difficult to clean.
Heat may also cause warping when cleaning printed circuit boards and can damage similarly delicate products.
For jobs involving heat-sensitive materials or running long ultrasonic cycles cooling coils connected to an outside water source and a temperature regulating device can be employed to keep temperatures in check.
The Role of Ultrasonic Frequency
At the beginning of this post we stated that chemicals, temperature, time and frequency are keys to safe, fast and efficient ultrasonic cleaning.
For best results the correct ultrasonic frequency comes into play. Most commercially available ultrasonic cleaners operate at a single frequency.
Ultrasonic frequency is given in kilohertz (KHz) or thousands of cycles per second – the vibration rate of generator powered ultrasonic transducers attached to the cleaning tank.
Ultrasonic frequency determines the size of the cavitation bubbles. Low frequencies such as 25 kHz create relatively large bubbles that deliver more vigorous cleaning action.
Higher frequencies such as 80 or 130 kHz deliver smaller bubbles. These produce a more gentle cleaning action better able to penetrate small holes and crevices unreachable by manual methods.
Examples include the benchtop ultrasonic cleaners from Elma. The Elmasonic E Plus series at 37 kHz, deemed the most practical for a vast majority of cleaning challenges.
Other models that operate at dual frequencies allow operators to select the best frequency for the job at hand. Examples of dual-frequency heated ultrasonic cleaners include the Elma P series, that switch between 37 and 80 kHz and industrial ultrasonic cleaners, exemplified by the TI-H series, that are offered at 25/45 or 35/130 kHz.
A Summary on Heated Ultrasonic Cleaners
In summary bath temperature plays a key role in ultrasonic cleaning. The optimum temperature is determined by the ultrasonic cleaning solutions employed and the items being cleaned.
While ultrasonic energy in itself creates heat, controllable heat is achieved by a heated ultrasonic cleaner that allows you to set the temperature best suited for the task at hand.
But as suggested in this post there is much more to be considered. That’s why you should contact the scientists at Tovatech who are ready to help you establish procedures to maximize the efficiency of your cleaning operations.