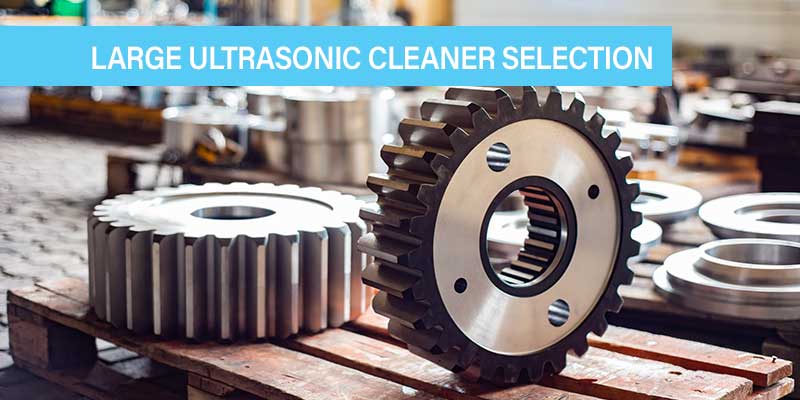
Selecting a Large Ultrasonic Cleaner for Large-Scale Cleaning
For businesses requiring the cleaning of large components or high-volume batches, a large ultrasonic cleaner with a capacity exceeding 100 gallons is essential. This guide outlines the critical features to consider when selecting a large ultrasonic cleaner, followed by practical application examples.
Key Features for Large Ultrasonic Cleaning Systems
- Optimal Tank Capacity:
- Tank size is paramount, encompassing both solution volume and physical dimensions (length, width, depth).
- Ensure parts are fully submerged, avoiding contact with tank walls or other parts.
- Utilize cleaning baskets for smaller items, with dividers and trays for efficient separation.
- For large components like engine blocks or heat exchangers, consider units with integrated supports and overhead crane compatibility.
- Targeted Ultrasonic Frequency:
- Frequency dictates cavitation bubble size and cleaning intensity.
- Lower frequencies (e.g., 25 kHz) are ideal for heavy contaminant removal from robust parts.
- Higher frequencies (e.g., 37, 45, 80, 130 kHz) provide gentler cleaning for delicate items.
- Dual-frequency systems offer versatility for diverse cleaning needs.
- Refer to our “how ultrasonic cleaners work” post for in depth frequency information.
- Durable Construction for Extended Operation:
- Industrial-grade units should feature welded, cavitation-resistant stainless steel tanks.
- Continuous operation capabilities for 8+ hour shifts are crucial.
- Automatic shut off timers protect the investment.
- Enhanced Mobility:
- Lockable wheels enable easy relocation within the facility.
- Temperature Control and Insulation:
- Integrated heaters maintain optimal cleaning solution temperatures.
- Insulated tanks and lids minimize noise, evaporation, and heat loss.
- Extended Cleaning Solution Lifespan:
- Implement weirs and spray bars for floating contaminant removal.
- Utilize single or dual filtration systems to capture solid contaminants.
- Select appropriate cleaning chemistries (demulsifying or emulsifying).
- See our cleaning solution selection guide for more information.
- Integrated Pre- and Post-Cleaning Rinse Options:
- Pre-cleaning removes coarse debris, extending solution effectiveness.
- Post-cleaning rinsing eliminates residual cleaning solution.
Examples of Large Ultrasonic Cleaners Offered by Tovatech
- Elmasonic xtra ST Floor-Mounted Cleaners:
- Dual-frequency (25/45 kHz) systems in 8 to 67-gallon capacities.
- Dynamic mode for alternating sweep and pulse cleaning.
- Optional filtration, pre-rinse, and post-rinse capabilities.
- SHIRACLEAN Wheel-Mounted Units:
- Capacities ranging from 25 to 204 gallons.
- Standard 40 kHz operation, with optional frequencies available.
- TVT and TVU models with varying features, including filtration, weirs, and covers.
- Options include power lift systems, rinse tanks, and heated air dryers.
- Custom Ultrasonic Cleaner Solutions:
- Tailored units designed to meet specific cleaning requirements.
- Considerations include part size, frequency, temperature, contaminants, and automation.
Applications for Large Ultrasonic Cleaners:
Additional Resources:
Get Expert Assistance from Tovatech
For personalized guidance in selecting the ideal large ultrasonic cleaner, please call or chat with our team of experts.