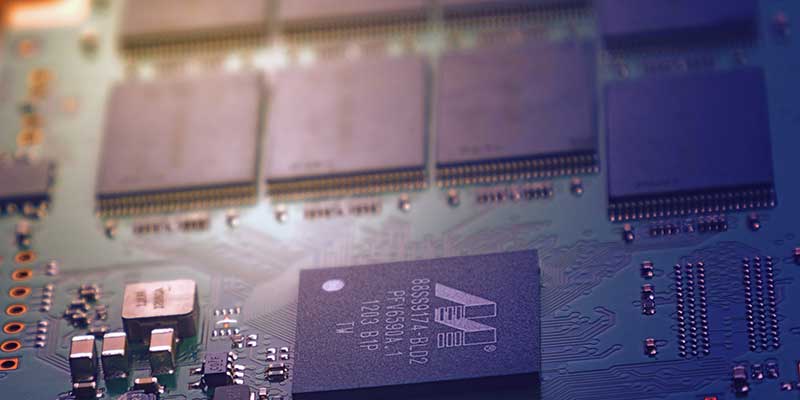
Ultrasonic PCB Cleaners for New and Reconditioned Boards
Removing soldering flux and residues from new PCBs and dirt when reconditioning PCBs by using an ultrasonic PCB cleaner is faster and more gentle than soaking and scrubbing with sprays and solvents. Manual PCB cleaning is time consuming, can damage delicate PCB assemblies and can be environmentally unfriendly. An ultrasonic PCB cleaner provides your best assurance that contaminants have been completely removed from new or reconditioned board configurations.
How an Ultrasonic PCB Cleaner Works
If you are familiar with ultrasonic cleaning proceed to the next section.
Ultrasonic cleaners come in a variety of sizes and capacities ranging from benchtop to floor mounted industrial units. Regardless of size, ultrasonic cleaners work in the same way.
A tank sized to accommodate objects being cleaned contains a biodegradable cleaning solution formulated for the task at hand.
Controls range from a simple on-off switch to more sophisticated timers, heaters and other features such as describe later in this post.
Ultrasonic transducers mounted to the tank and connected to a generator create billions of microscopic vacuum bubbles that implode on contact with the PCBs in a process called ultrasonic cavitation. This effectively strips away all contaminants from all surfaces without damaging the PCB components*. Depending on the number and complexity of the PCBs the process can be completed in as little as 10 – 15 minutes.
For more information on this process check our post on how ultrasonic cleaners work or visit our ultrasonic cleaning learning center.
Selecting your Ultrasonic PCB Cleaner
As noted above, ultrasonic cleaners come in a variety of sizes and capacities. When selecting your ultrasonic PCB cleaner keep in mind that cleaning is accomplished in baskets, with dimensions slightly smaller than the tank dimensions. Boards should be positioned vertically in the basket in such a way that they are not in contact with each other.
As an example, we suggest the Elmasonic E Plus series of cleaners offered in 9 tank sizes from 0.25 to 7.5 gallons.
The E Plus line is designed to thoroughly cleans a broad range of parts made of metal, glass or plastic.
It features a permanent Sweep mode to provide fast and uniform cleaning, avoiding potentially damaging “hot spots” and low- or no-cavitation “dead zones.” Activate the Pulse mode to remove stubborn deposits on the PCB boards and to degas fresh ultrasonic cleaning solutions.
A timer lets you program the length of the cleaning cycle to 30 minutes or continuous, allowing you to attend to other matters. Set the recommended cleaning temperature up to 80⁰C.
Selecting your Ultrasonic PCB Cleaner Solution
Today you can select from a broad range of ultrasonic cleaning solution formulations. Most are available in concentrates and are biodegradable. Biodegradability removes to a large extent earlier concerns regarding disposing spent solutions.
For PCB cleaning we recommend elma tec clean A1 formulated to clean PCBs, mother boards, electronic parts, fine optics and plastics.
Elma tec clean A1 should be diluted to 3 to 10% with water before use. For example, a 2.5-liter bottle dilutes with water to 15 gallons of 5% solution for PCB cleaning. It is formulated to leave no chemical residue after rinsing with distilled or deionized water.
A Suggested PCB Cleaning Cycle
As with most ultrasonic cleaning procedures, you’ll develop your own routine for PCB cleaning based on your particular requirements. Here is a suggested way to begin:
- Fill the cleaning tank with water then add the correct amount of cleaning solution formulation based on tank capacity. Do not overfill the tank – usually designated by a “fill line”.
- Turn on the unit without a load to mix and degas the solution. Degassing removes air trapped in the liquid, which can extend cleaning time. Activating the Pulse mode on the Elmasonic E Plus units speeds the process. Some ultrasonic cleaner models may be equipped with a Degas mode for this function.
- Set the correct temperature. For cleaning PCBs using elma tec clean A1 65⁰C is suggested.
- Place the boards vertically in a basket or rack in such a way that they do not contact each other. When ready lower the basket into the solution. Use the cover to reduce noise and evaporation.
- At the end of the cycle remove and inspect. When satisfied rinse the boards with de-ionized water to thoroughly remove cleaning solution residues and allow them to dry.
Solder Flux Disposal
As suggested above, spent biodegradable cleaning solutions may be safely drained to sanitary sewers by following your local regulations.
Flux residues are another matter. These must be isolated from the cleaning bath and disposed of in a proper manner.
Soldering flux contaminants that rise to the surface can be skimmed off and stored for later disposal.
Industrial ultrasonic PCB cleaners used large-scale manufacturing can be equipped with diverter valves allowing operators to direct floating contaminants or those that settle to the bottom of the tank to filtration systems, returning treated solution to the cleaning bath.
Tanks fabricated with sloping bottoms facilitate collection of settled fluxes for routing to the filtration system.
Eventually, however, PCB cleaning time will increase as the solution loses its effectiveness. It must be replaced. Drain the tank and dispose of the spent solution according to local regulations. Take this time to clean the tank following directions in the instruction manual.
Fill the tank with fresh solution and proceed as above.
In Conclusion
We hope this post is helpful. Contact the ultrasonic cleaning professionals at Tovatech to discuss PCB cleaning equipment, solutions and solution maintenance options tailored to your production requirements.
*Ultrasonic PCB cleaning cannot be used when boards contain sealed board-mounted relays.