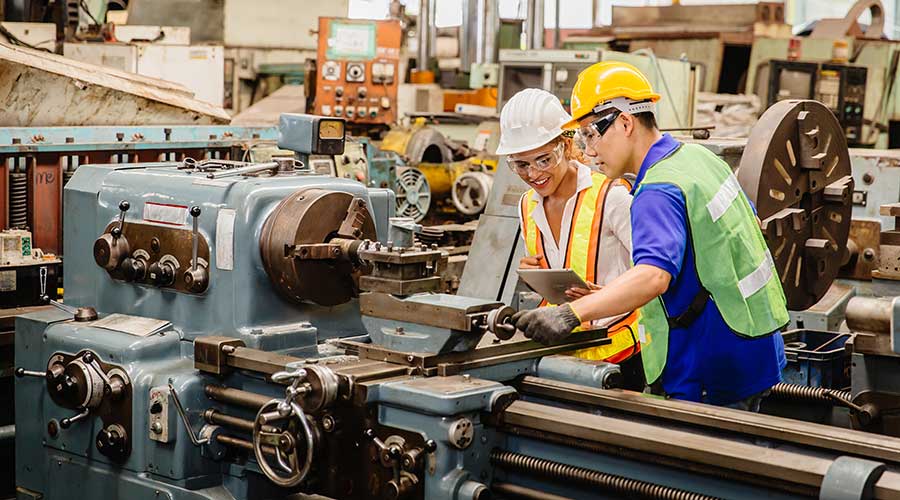
Avoid Product Damage by Ultrasonic Waves
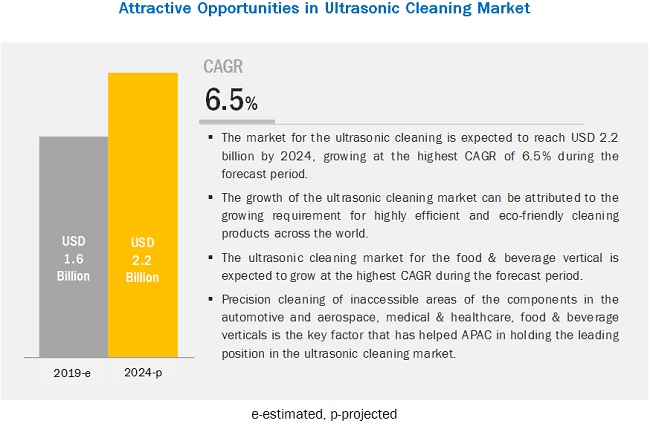
The worldwide acceptance of ultrasonic cleaning is confirmed by a MarketandMarkets report stating that it is expected to grow from USD 1.6 billion in 2019 to USD 2.2 billion by 2024, at a CAGR of 6.5% during the forecast period. That report describes reasons driving the growth rate while this post provides important tips on avoiding product damage by ultrasonic waves.
Ultrasonic Waves Described
Ultrasonic waves is another way of describing what is called cavitation action in an ultrasonic cleaner tank. Cavitation action results from the violent implosion of millions of microscopic bubbles every second.
These implosions create a temperature of 5000˚C (>9000˚F) and a jet of plasma impacting the objects being cleaned. It is cavitation action by ultrasonic waves that quickly strips away dirt and other contaminants from parts being cleaned.
Note that this action is exceedingly fast meaning it does not damage the parts. But over time it will increase the temperature of the ultrasonic cleaning bath.
How Ultrasonic Waves are Created
They are created by ultrasonic transducers bonded to the cleaning tank. These in turn are driven by an ultrasonic generator operating at a set frequency, examples being 40 kHz at a lower level and 130 kHz at an upper level.
Some ultrasonic cleaners offer user-selected dual frequencies. Benchtop example is the P series offered and the floor mounted x-tra ST models.
Lower frequencies create more vigorous cleaning action than higher frequencies. Because of this, they are generally used for removing coarse contaminants. Higher frequencies are used for cleaning products that are more delicate or have highly polished finishes.
This helps explain why using correct ultrasonic waves is important to avoid damaging products you are cleaning.
More on Ultrasonic Waves and Product Protection
From the above, you’ll understand that while properly operated and controlled ultrasonic cleaning is generally safe for a wide range of products, a key criterion being “properly operated.”
In addition to selecting the correct ultrasonic frequency we include a combination of the cleaning solution chemistry and cleaning bath temperature. The guiding factor is the items being cleaned and what is being removed.
This suggests that ultrasonic cleaning does have the potential to damage products, and why expert advice should be sought when operating an ultrasonic cleaning system, especially if the parts being cleaned are of an unusual dimension or composition. Nevertheless, some basic rules generally apply.
Ultrasonic Cleaning Solution Formulations
Ultrasonic cleaning solutions, for example, are formulated for specific cleaning operations. Solution selection is based on what is being cleaned, the contaminants removed, the product configuration, its composition and post-cleaning requirements.
The pH of a solution – acidic, neutral or alkaline – is also an important consideration, the selection of which is likewise governed by what is being cleaned and what is being removed. For more information on this see our page on ultrasonic cleaning solution formulations and applications.
Other Factors Impacting Safe Ultrasonic Cleaning
Parts Positioning
Ideally parts placed in the ultrasonic cleaning basket should not be in contact with each other. While this may necessitate several cleaning cycles, it will avoid vibration damage to the parts.
Cleaning Time
A great benefit of today’s ultrasonic cleaners is that they allow you to set your cleaning parameters then set cleaning cycle timer to shut off the unit at the end of the cycle. This relieves you of the need to monitor the unit. As you develop experience you’ll be able to set the timer and attend to other tasks while the ultrasonic waves do their job.
Frequency Selection
As noted above, delicate or highly polished surfaces on materials such as glass and aluminum should be cleaned at high frequencies such as 130 kHz to avoid being damaged by the more aggressive cavitation action at 37 or 40 kHz.
The Sweep Mode
Even with the proper ultrasonic frequency damage is possible because under a Normal mode the ultrasonic waves create fields of relatively high, low and no energy in the bath.
These are called standing waves. It means that surfaces receive uneven intensities of cavitation, which manifests itself in streaks of microscopic erosion. Note that ultrasonic cleaners operating in or set for the normal mode find application in sample preparation and related activities in the lab.
To counteract this, a Sweep mode is engaged to distribute the cleaning action more evenly in the bath. This is accomplished automatically by continuously shifting the frequency over a narrow range.
The Sweep mode proves useful across the broad spectrum of ultrasonic cleaning operations in terms of increasing efficiency. But it also helps protect very thin or delicate parts such as printed circuit boards that might begin to vibrate at the same resonance frequency of the transducers and shatter or otherwise be damaged.
The Degas Mode
Fresh cleaning solutions contained entrapped air that interferes with ultrasonic wave action until the air is removed. This can be done more quickly if your ultrasonic cleaner is equipped with a Degas mode. Otherwise operate the unit for a period of time without a load to drive off trapped air.
The Pulse Mode
If you frequently clean heavily soiled parts or remove tenacious contaminants using ultrasonic waves select an ultrasonic cleaner offering a Pulse mode. Activating it provides a 20% boost in ultrasonic wave action to blast away contaminants. An example is the Elmasonic P line, which also offers dual frequencies, variable power and other useful features including
Variable Power
This is a complex subject covered in our post on ultrasonic frequency, power and time. While you may think that more power means better results from ultrasonic waves, such is not the case. This post describes why this is so.
Other Suggestions
To avoid damage, metal parts being cleaned in the same cycle should be of the same composition, and ideally should not be in contact with each other.
Otherwise, most anything that can be safely wetted can be cleaned by ultrasonic waves when you employ proved procedures.
And finally, contaminants removed during cleaning remain in the bath, and will degrade performance over time.
Using Ultrasonic Waves: Practice makes Perfect
We suggest you conduct a series of trial runs to determine the optimum operating parameters before initiating full-scale cleaning operations with your ultrasonic cleaner.
We at Tovatech hope these points prove helpful in avoiding damage that can result from improperly operated ultrasonic cleaning baths. Contact our professionally trained ultrasonic cleaning specialists for recommendations on equipment and procedures tailored to your specific needs.