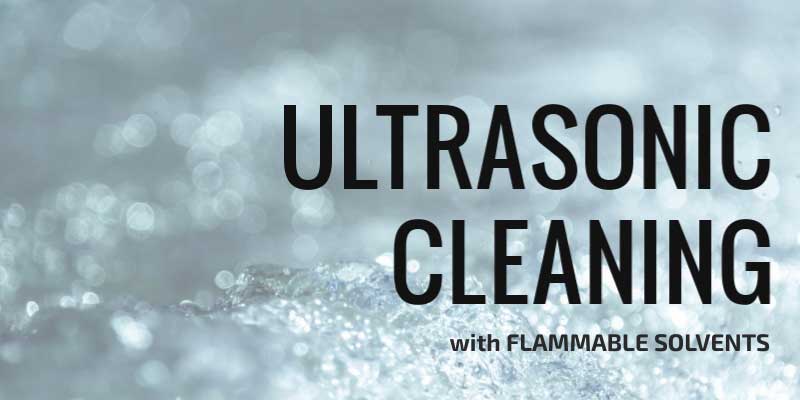
How to Safely Use a Solvent Cleaner
As described in Chapter 3 of the Adhesives Technology Handbook*, “solvent cleaning is the process of removing soil from a surface with an organic solvent without physically or chemically altering the material being cleaned. This includes methods such as vapor degreasing, spraying, immersion, and mechanical or ultrasonic scrubbing.” This post describes how to safely use a volatile solvent cleaner with a low flash point.
Solvent Cleaner Flash Points
Solvent cleaners have different flashpoints. In chemistry, the flash point of a volatile material is the lowest temperature at which its vapors ignite if given an ignition source. In brief, the lower the flashpoint the more flammable they are. This is important when using a solvent cleaner.
The American Chemical Society publishes a table of common organic solvents that includes flash points. Examples of low flash point volatile solvents are 1-propanol at 59⁰F (15⁰C), acetone at -4⁰F (-20⁰C) and toluene at 39⁰F (4⁰C).
Using a Solvent Cleaner in an Ultrasonic Cleaner
Ultrasonic energy is widely recognized as a fast, safe and efficient way to remove unwanted contaminants from most any surface that can be safely wetted.
Using a flammable solvent in an ultrasonic cleaner may be necessary if conventional biodegradable cleaning solution formulations won’t do the job.
But as the name indicates, a flammable solvent cleaner gives off vapors that are both unhealthy for personnel and may be explosive. Vapor generation is greatly increased due to cavitation action in the ultrasonic cleaner tank.
Dealing with Flammable Solvents in an Ultrasonic Cleaner
Local and national regulations apply when using a solvent cleaner.
As a general rule, whenever you operate an ultrasonic unit using a solvent cleaner you must check with local public safety officials and your plant safety personnel to ensure compliance.
Your best overall source for compliance, in addition to your local and plant safety personnel, is the National Electric Code (NEC) and National Fire Protection Association (NFPA). These address issues related to Class, Division and group, ventilation, electrical cord , plug , and receptacle. Check this link to NFPA 30 for more information on these issues.
There are correct procedures for using a solvent cleaner for an ultrasonic cleaning operation. The simplest and least costly approach can be used to clean small parts in benchtop ultrasonic cleaner beaker kits available from Tovatech.
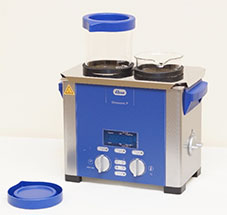
This approach, however, does not preclude careful handling of solvent cleaners and using them in well-ventilated areas.
As a preparatory step fill the ultrasonic cleaner tank with water containing a surfactant to improve cavitation efficiency. Activate the ultrasonic cleaner’s degas function to remove entrained air in the solution, otherwise operate it until air bubbles not longer rise to the surface.
Place parts to be cleaned in beakers or flasks. Then add enough cleaning solvent to fully immerse the parts. Loosely cap the container to slow the escape of solvent vapors. Do not tightly cap the containers.
A tank lid with openings to snugly accommodate the containers is put in place. Otherwise use a shallow-draft mesh basket. Lower the containers into the tank taking care that they are immersed 2 to 3 inches into the solution. Containers should not contact the bottom the tank.
Activate the ultrasound. Cavitation action in the aqueous solution will penetrate the container walls to activate the solvent cleaner and clean the products.
At the end of the cycle decant the solvent into a sealable container for reuse or for disposal according to local regulations. Because most solvents rapidly evaporate there may be no need to rinse and dry the cleaned products unless your procedures call for it.
Large Scale Ultrasonic Cleaning with Flammable Solvents
Specially designed and code-approved ultrasonic cleaners are required when cleaning large parts using flammable solvents in the tank itself.
An example is the SOL XP explosion proof ultrasonic cleaner available from Tovatech.
Available in 6 tank capacities from 2 to 33 gallons, these explosion proof bench top ultrasonic cleaners are fast, efficient and safe to use for solvent cleaning using isopropyl alcohol, acetone and similar low flash point formulations.
They provide the ultrasonic power density of the largest industrial systems, and are designed for use in Class I Division 1 hazardous areas.
These explosion proof ultrasonic cleaners carry an Intertek ETL Certification and are shipped with a remote electrical panel to be located outside the CID1 envelope. Units are nitrogen inerted for additional fire protection. Other included and optional features can be found on Tovatech’s SOL XP flammable liquid ultrasonic cleaning systems page.
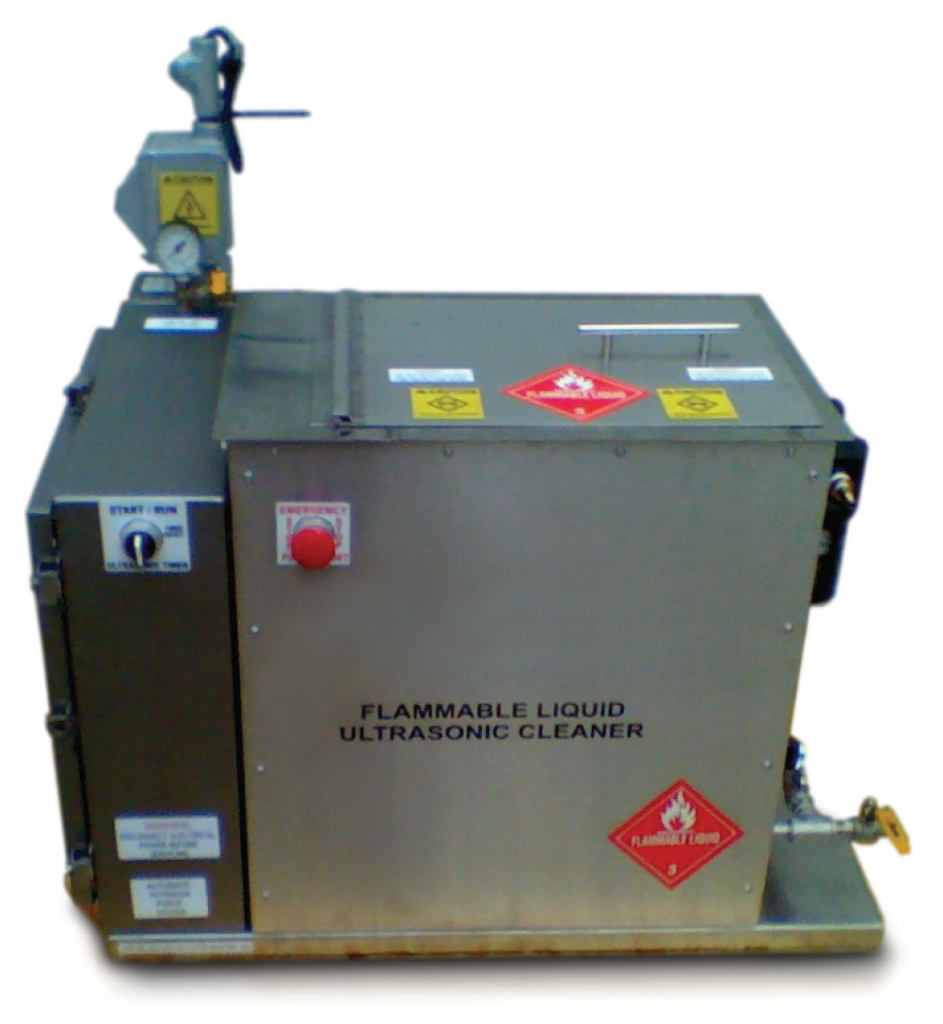
Examples Using the SOL XP Solvent Cleaner
An explosion-proof ultrasonic cleaning system satisfies customers’ preferences for flammable solvents employed during initial cleaning processes for new and reconditioned stainless-steel filters at Porvair Filtration Group in Caribou, ME.
Solvent cleaning is part of the passivation cycle to improve the corrosion resistance of 316L stainless steel filters by removing ferrous contaminants like free iron from surfaces, and restoring them to their original corrosion specifications.
At L3 Harris EDD (Electron Devices), Torrance, CA, solvent ultrasonic cleaning is used to remove machining oils and particulates from piece parts and brazed assemblies at various stages of the assembly process including preparing surfaces for a subsequent coating. The company manufactures products such as traveling wave tubes, xenon ion propulsion systems, electronic power conditioners and microwave power modules for a variety of space and defense applications.
An Automated Process for Solvent Cleaning Very Small Parts
Extremely small parts such as watch parts, micro-optics, and micro-machined parts are very effectively cleaned, rinsed, and dried in the Elmasolvex VA ultrasonic cleaner.
This ultrasonic cleaner is certified to be explosion proof when used with solvents with a flash point ≥ 12°C (53⁰F). Optimum cleaning results are achieved using a combination of multi-frequency ultrasonic cleaning, oscillation, and vacuum technology. Cleaned parts are completely residue-free.
View this video for a short tutorial on how it works.
Need more Solvent Cleaner Info?
Contact the ultrasonic cleaning professionals at Tovatech for help in specifying the correct ultrasonic cleaner for your applications.
——————
*Third Edition 2015 “Material Surface Preparation Techniques”