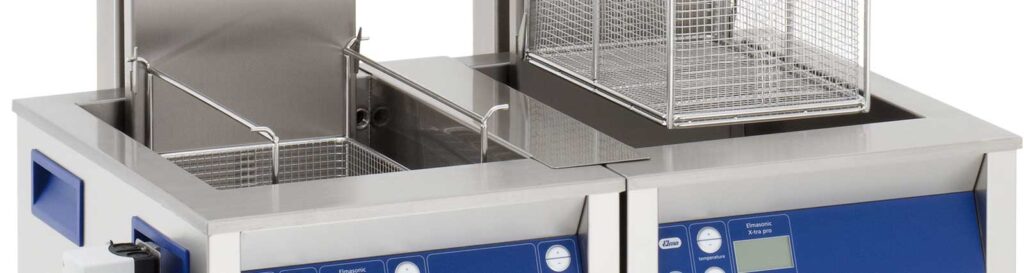
Ultrasonic Cleaning Tanks: What You Should Know
While a variety of ultrasonic cleaners are the market, one component they have in common is the ultrasonic cleaning tank where cleaning action takes place. Whether you select a basic model ultrasonic cleaner, an advanced benchtop or a floor-mounted industrial-scale model, long-term reliability depends on the industrial ultrasonic cleaning tank and how you use and care for this essential component.
Ultrasonic Cleaning Tank Size
Cleaning tank size – which also governs the cleaning solution capacity – must be sufficient to accommodate whatever you are cleaning in such a way that parts are fully immersed in the ultrasonic cleaning solution.
Although this may seem a no-brainer, remember that parts being cleaned must not be in contact with each other or the tank itself. Otherwise, parts can be damaged, and perhaps more seriously, the tank itself can be damaged due to ultrasonic vibration.
That is why most cleaning is accomplished in baskets, the dimensions of which are slightly under the tank length, width, and depth dimensions.
Basket Size vs. Cleaning Tank Size
Baskets are sized to suspend parts at the ideal point above the bottom of the tank as well as the distance to the tank walls. That’s why manufacturers such as Elma recommend the correct basket for each ultrasonic cleaner tank size offered.
The distance from the bottom of the basket to the surface of the cleaning solution defines the working depth of the solution, which must be sufficient to completely immerse items being cleaned.
Note that while baskets are commonly suspended by handles resting on the tank rim others are equipped with rubber-coated feet. These are positioned near the corners of the tank bottom where there is minimal vibration.
Exceptions to Ultrasonic Cleaning Baskets
Large capacity industrial ultrasonic cleaner tanks can be fitted with bottom racks on which parts rest during the cleaning cycle. In other cases, parts can be lowered into the cleaning solution by an overhead suspension system.
Ultrasonic Cleaning Tank Fabrication
Ultrasonic cleaner tanks such as the Elmasonic E Plus series used for non-industrial service should be fabricated of cavitation-resistant stainless steel. Look for rounded pressed or smoothly welded corners.
Tanks for benchtop or floor-mounted industrial ultrasonic cleaning tanks such as the Elma x-tra TT benchtop units designed for long-term cleaning cycles should be fabricated of heavy-gauge stainless steel.
Drains on ultrasonic cleaning tanks facilitate removing spent cleaning solutions, a point covered later in this post.
Consider lids to reduce operation noise and cleaning solution evaporation. Certain models have lids that when inverted double as drain trays for parts after baskets are removed from the cleaning solution.
Industrial ultrasonic cleaner tanks may have insulated lids offered as an option.
Maintaining Your Ultrasonic Cleaner Tank
As noted earlier, stainless steel is the preferred material of construction for industrial ultrasonic cleaning tanks. That’s because of its high resistance to cavitation action and chemical attack by ultrasonic cleaning solutions.
That said, highly acidic cleaning solution chemistry should only be used in acid-resistant tubs that can be immersed in a water solution to which a surfactant is added. Ultrasonic waves pass through the acid resistant container to act on objects being cleaned in the acidic solution.
Takeaway: Do not use aqueous cleaning media with pH values in the acid range (pH < 7) directly in the ultrasonic cleaner tank if fluoride, chloride, or bromide ions are present or can be released from parts being cleaned. These can quickly destroy stainless steel by crevice corrosion within a very short period of ultrasonic operation.
For more on cleaning solution chemistry please check our post on cleaner solution selection tips.
Dealing with Cleaning Solution Contaminants
Contaminants removed during ultrasonic cleaning must go somewhere and that “somewhere” is in the cleaning solution itself. This is why solutions must be drained and replaced (and the tank cleaned) on a regular basis.
For some operations replacement time is signaled by visibly dirty solutions and longer cleaning processes. In others, notably the removal of grease and oils, it is evidenced by oils rising and floating on the surface.
Contaminants that rise to the surface are less likely to cause tank damage but must be removed to prolong cleaning solution efficiency.
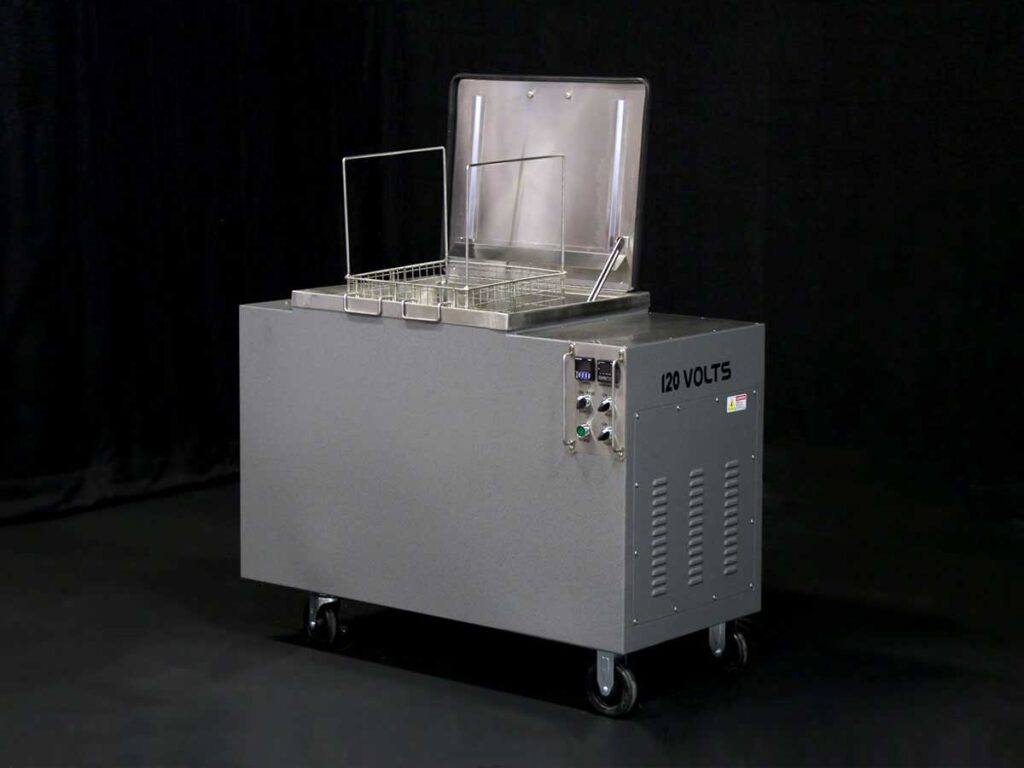
Skim them off and set them aside for later disposal, thereby prolonging the lifetime of the solution.
Larger industrial-sized ultrasonic cleaners such as the Shiraclean line available from Tovatech can be equipped with a filtration system and a skimming ledge that channels the contaminants into a holding tank for proper disposal.
Not as evident are hard particles that fall to the tank bottom and can severely damage tanks as ultrasonic vibrations cause them to act as a “drill” eventually creating pinholes in the tank allowing cleaning solutions to drain into the ultrasonic cleaner electronics.
Whatever the case, over time cleaning solutions will lose efficiency and must be replaced.
Cleaning Tank Discoloration
Tank discoloration, also called furring, can show up in a variety of colors in an ultrasonic tank. It can occur if the unit’s heater is activated when the ultrasound is not activated. This causes the solution adjacent to the heater to reach very high temperatures resulting in tank discoloration.
A Summary on Ultrasonic Cleaning Tank Maintenance
Contaminants removed during the ultrasonic cleaning process end up in the solution and eventually degrade its performance, necessitating replacement.
For most bench top ultrasonic cleaners a good practice is to skim off and properly dispose of contaminants that float to the surface.
Larger cleaners such as the Shiraclean units may have sprayers and skimming weirs that direct floating contaminants into oil skimmers or oil separators for either disposal or recycling.
Contaminants that drop to the bottom of a tank can be directed through filtering mechanisms that return treated solution to the tank.
These, then, are key components that together closely relate to your specification criteria for industrial ultrasonic cleaning tanks.
We invite you to view the videos on our ultrasonic cleaning learning center and contact the scientists at Tovatech for unbiased recommendations on specifying and maintaining your ultrasonic cleaning equipment and cleaning solution chemicals.