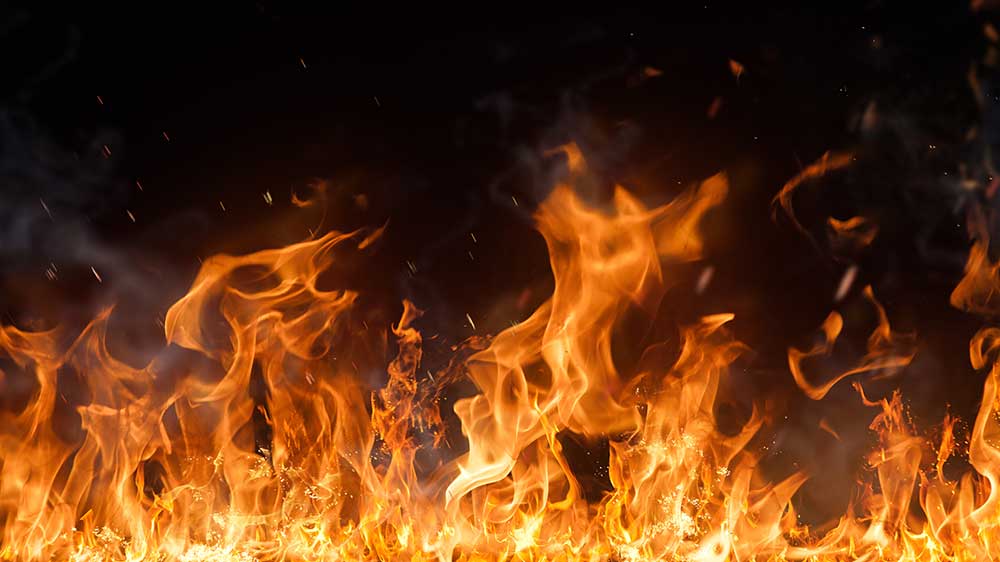
Selecting an Explosion Proof Ultrasonic Cleaner
Specify an explosion-proof ultrasonic cleaner when a low flash point volatile solvent is required to achieve the desired cleaning results. Unlike aqueous solutions with non-volatile components, flammable solvents do not leave a residue behind upon drying.
Why Does the Ultrasonic Cleaner Need to be Explosion Proof?
Flash point is the temperature at which a particular organic compound gives off sufficient vapor to ignite in air when given an ignition source. Louisiana State University published a table of common organic solvents and their flash points. Examples of low flash point volatile solvents requiring an explosion-proof ultrasonic cleaner are isopropyl alcohol at 53⁰F, acetone at -4⁰F and toluene at 40⁰F.
In view of this, an ultrasonic tank filled with a low flash point solvent must be explosion proof because the solvent will evaporate during the cleaning process producing a vapor cloud. Moreover, the heat generated by the ultrasonic cleaning process accelerates solvent evaporation and vapor generation. The ultrasonic generator and transducers can act as ignition sources leading to a fire or explosion.
An explosion proof ultrasonic cleaner isolates these components from the solvent vapor so that ignition is not possible. Any switches on the model are intrinsically safe; they don’t have enough power to act as ignition sources.
Although the explosion proof ultrasonic cleaner itself will not catch fire or explode, it will release flammable vapor into the surrounding environment. Depending on the distance from the tank, the nearby area will have a hazardous area rating of Class I Division 1 or Class I Division 2 (as defined by NFPA). Precautions are called for when positioning your explosion-proof ultrasonic cleaner. This can be mitigated by situating the tank in a suitable fume hood.
Explosion Proof Ultrasonic Cleaner Applications
- Medical devices such as surgical implants are frequently cleaned using IPA because it evaporates quickly, is relatively non-toxic, and residue-free.
- Use IPA or acetone to remove ferrous contaminants from new and reconditioned stainless steel filters as part of passivation cycle to improve corrosion resistance.
- Remove machining oils and particulatesfrom traveling wave tubes, xenon ion propulsion systems, electronic power conditioners and microwave power modules at various stages of assembly.
- Clean small X-ray tube components in a volatile solvent for absolutely contamination-free results.
- Remove solder flux and other contaminants to avoid mechanical brushing damage to PCBs and other delicate assemblies.
- Clean adhesive gun and spray painting nozzles to assure quality coatings.
- Remove dry ink residues and contaminants from inkjet print head parts and nozzles in coding and labeling equipment.
Explosion-Proof Ultrasonic Cleaner Options
Here are three equipment options when using flammable solvents for ultrasonic cleaning:
Flammable Solvent Beaker Kits
Explosion proof ultrasonic cleaners are significantly more expensive than conventional models. When cleaning small parts, it may be possible to safely use a conventional ultrasonic cleaner by using a secondary container instead of placing the solvent directly in the tank. Flammable solvent beaker kits are a good choice when parts are relatively small and cleaning is done on an occasional basis. This option should be conducted in areas with sufficient ventilation to prevent solvent vapor accumulation.
Place parts in a beaker and add enough solvent to ensure they are fully immersed. Loosely cover the beaker to minimize escaping vapor during the cleaning process.
In this instance you can use tap water with a surfactant such as a few drops of liquid dishwashing soap in the ultrasonic cleaning tank. Degas the solution before proceeding by selecting the degas mode. If the unit doesn’t have a degas mode, operate the ultrasonic power for about 20 minutes to degas.
Beakers can be supported in the ultrasonic bath using a beaker-supporting cover instead of a basket. The bottom 1-2 inches of the beakers should be immersed in the water. Ultrasonic energy penetrates the glass walls and cavitation occurs in the solvent.
Use an Explosion-Proof Ultrasonic Cleaner
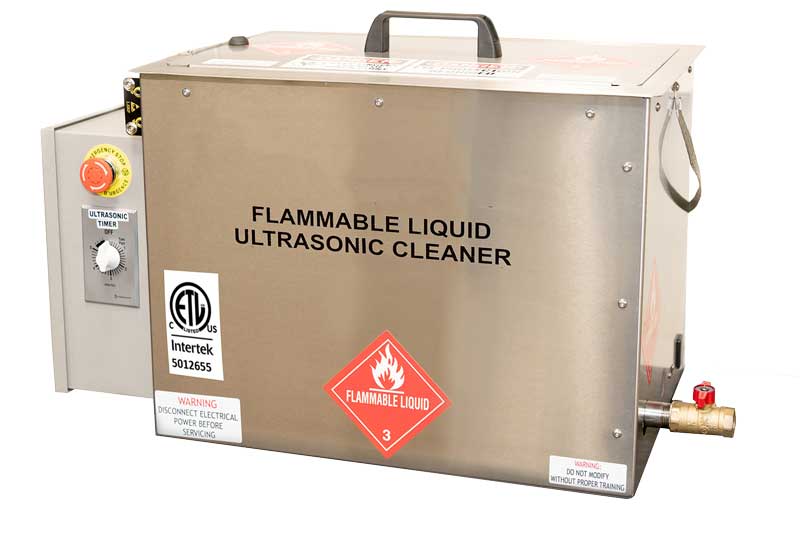
For large scale operations consider SOL XP flammable liquid ultrasonic cleaning systems in 2, 4, 6, 9, 15, 24 and 33 gallon tank capacities.
These 40 kHz ultrasonic frequency units are compliant with all Class I, Division 1 (CID1) code and zone requirements. Different only in tank dimensions and capacities they can be fitted with a cooling jacket around the upper tank perimeter to capture solvent vapor and reduce odor.
The SOL XP ultrasonic cleaners come with Intertek ETL Certification and are shipped with a remote electrical panel to be located outside the CID1 envelope.
Units are nitrogen inerted for additional fire protection and have other included and optional features.
An Explosion Proof Ultrasonic Cleaner for Very Small Parts
Extremely small parts such as watch parts, contact lenses, micro-optics, and micro-machined parts are effectively cleaned, rinsed and dried in the Elmasolvex VA ultrasonic cleaner.
This explosion proof ultrasonic cleaner is certified when used with solvents with a flash point ≥ 12°C (53⁰F). Optimum cleaning results are achieved by combining multi-frequency ultrasonic cleaning, oscillation, and vacuum technology. Cleaned parts are completely residue-free.
Other Safety Precautions when Using Flammable Solvents
As noted earlier operating ultrasonic equipment when cleaning with flammable solvents may create what is called a hazardous area due to the solvent and fumes.
Ventilate fumes using approved ventilation systems. Electrical equipment, wiring, lighting fixtures, outlets and similar equipment must be rated as intrinsically safe by the National Electric Code, NFPA-70 if situated within the hazardous envelope.
Questions? Need More Info?
Chat or call the ultrasonic cleaning professionals at Tovatech for information on selecting and using an ultrasonic cleaner with flammable solvents.
Looking for other information about ultrasonic cleaners? Here are some other topics you may find of interest: